Are your warehouse workers spending too much time walking back and forth, picking items for individual orders? This inefficiency can slow down operations and increase costs.
If you're looking for a more streamlined solution, batch picking could be the answer.
This method groups similar orders together, allowing pickers to gather multiple items in one go, saving time and boosting productivity.
Let's dive into what batch picking is, how it works, and why it might be the perfect fit for your warehouse operations.
What is Batch Picking?
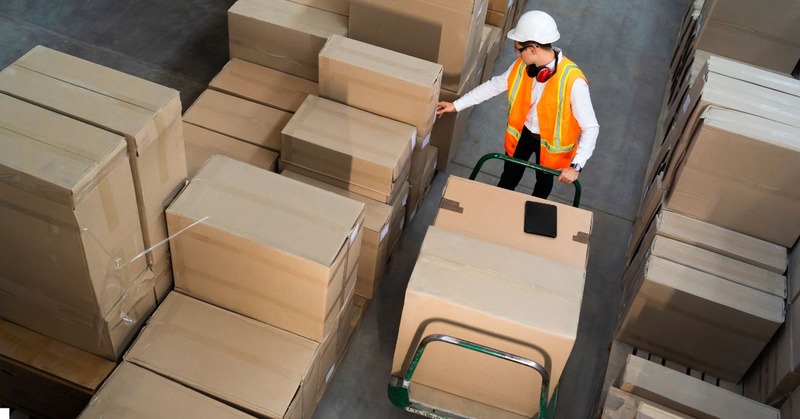
Batch picking is a strategic approach used in warehouses to enhance the efficiency of the order fulfillment process. This method involves grouping multiple orders with similar characteristics into batches for simultaneous picking, rather than processing each order individually. It's akin to doing grocery shopping for several lists at once, ensuring that each trip down the aisle is maximally productive.
How It Works
Here’s a general overview of how batch picking works:
Generate Picking Lists
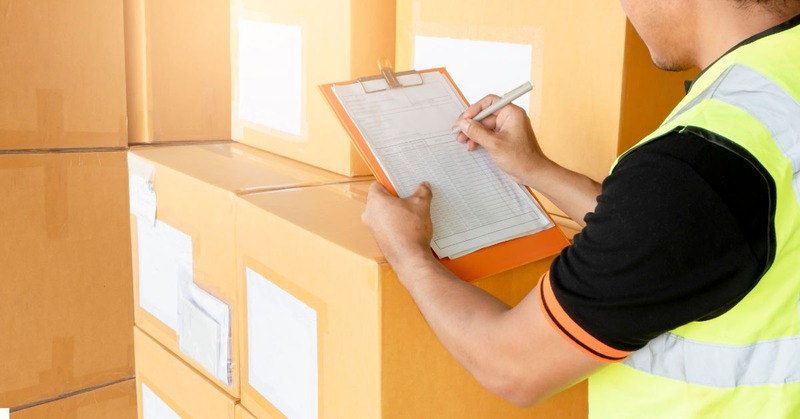
The first step in batch picking involves creating detailed picking lists that specify the items to be picked, their quantities, and their storage locations.
These lists are usually generated using a warehouse management system (WMS) or an order management system (OMS), which helps in organizing orders into efficient picking batches.
Prepare and Equip Pickers
Once the picking lists are ready, pickers are assigned and equipped with the necessary tools for the task. This might include totes, carts, and mobile scanners.
Some setups also utilize advanced technology like voice-picking headsets, which provide real-time directions to pickers, guiding them to the locations of items within the warehouse.
Picking the Items
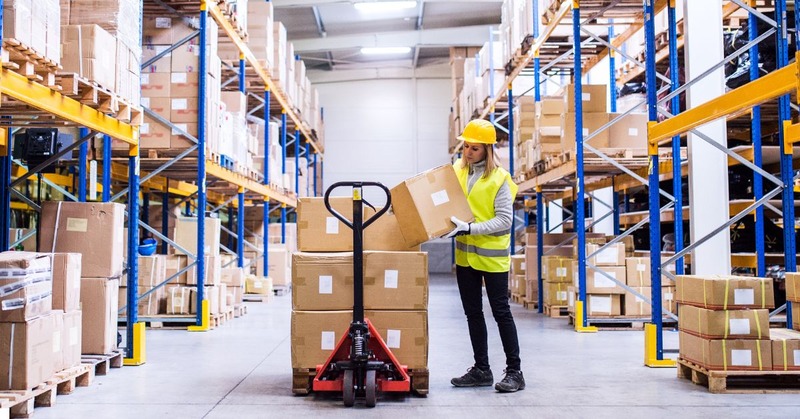
Pickers follow their lists to collect items from the warehouse. The process is optimized to minimize unnecessary movements; for example, if several orders contain the same item, the picker collects them all at once, reducing the need to revisit the same location multiple times.
The actual collection method may vary, such as picking directly into shipping boxes or using separate bins for each order within a cart.
Sorting and Shipping
After all items in a batch have been picked, they are taken to a sorting area.
Here, items are organized into their respective orders. If not already sorted during the picking phase, this is where items are placed into their final shipping containers, ready for dispatch.
Efficient sorting is crucial to maintain the integrity of each order and ensure timely delivery.
Why Consider Using Batch Picking?
Batch picking streamlines warehouse operations and offers several benefits:
Efficiency and Time Savings
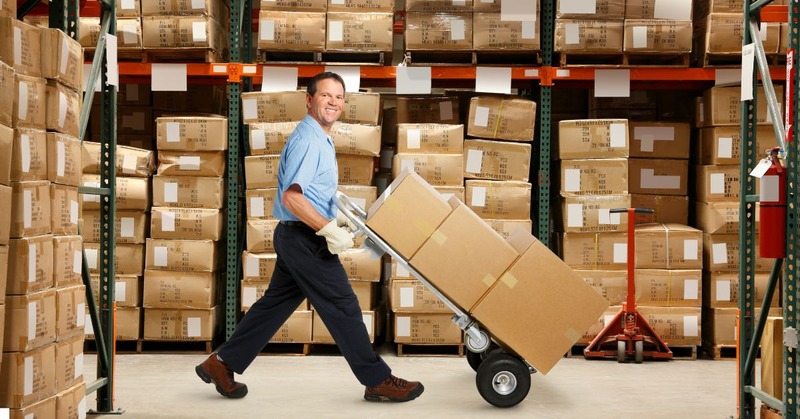
Batch picking reduces travel time by allowing pickers to handle multiple orders in one go. This streamlined approach saves time and reduces labor costs, making operations more efficient.
Improved Accuracy and Customer Satisfaction
This method minimizes picking errors, leading to more accurate orders. Fewer errors mean higher customer satisfaction, as it reduces the likelihood of shipping discrepancies and customer complaints.
Cost-Effectiveness
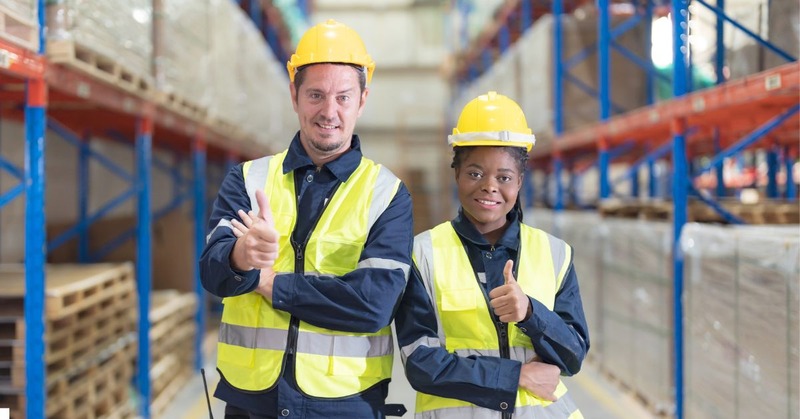
Batch picking lowers operational costs by reducing unnecessary movements and optimizing workforce usage. This efficiency translates into significant cost savings for warehouse operations.
These reasons are why you should consider incorporating batch picking into your picking operations. Next, we'll explore how batch picking differs from other picking methods.
How Does Batch Picking Differ From Other Picking Methods?
Single Order Picking
Unlike batch picking, which consolidates multiple similar orders into a single picking activity to minimize walking and maximize efficiency, single order picking focuses on one customer's order at a time.
This method can result in extensive travel time within the warehouse as each order's items are collected individually, making it less efficient in environments where many orders share common items.
Multi-Batch Order Picking
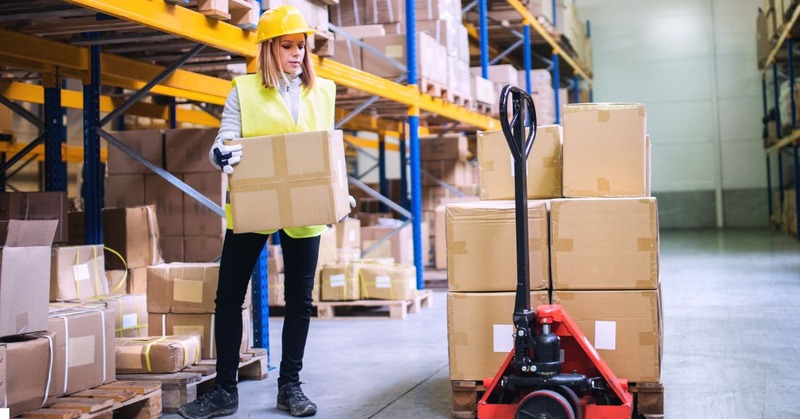
Multi-batch order picking differs from standard batch picking by not just grouping similar orders together but also continuously processing multiple batches in sequence.
This method is designed to optimize productivity by keeping pickers continuously active, moving from one batch to another without pause, which can enhance throughput more than the standard batch method where batches are processed one at a time before the next is set up.
Cluster Picking
Cluster picking uses a cart with compartments for different orders, allowing a picker to fill several orders on a single warehouse pass.
This contrasts with batch picking, where items for multiple orders are gathered but are generally homogeneous, requiring sorting after the pick.
Cluster picking reduces sorting time by allocating each item directly to its designated order during the picking process.
Wave Picking
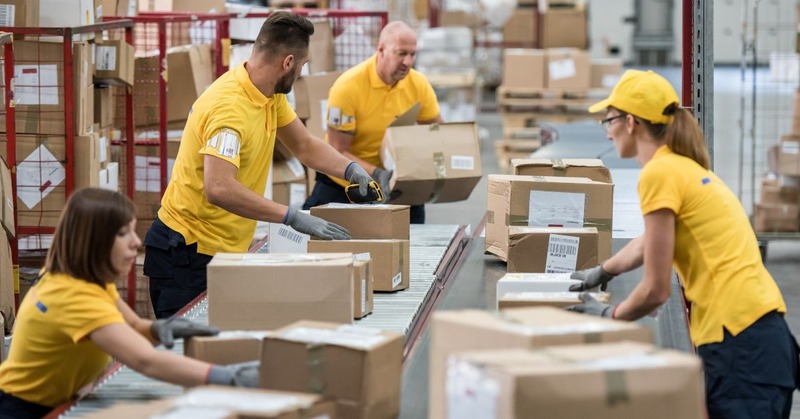
Wave picking organizes picks into specified intervals or "waves" to align with shipping schedules or labor availability.
This method can integrate both zone and batch picking but does so in a tightly controlled timeframe to optimize shipping and labor.
Batch picking, by contrast, is generally continuous and lacks the temporal segmentation of wave picking, focusing instead on reducing travel times by grouping similar order items regardless of shipping schedules.
ALSO READ: Wave Picking vs Batch Picking: Which Picking Method is Better?
Zone Picking
Zone picking confines pickers to specific areas of the warehouse, reducing their travel distance but possibly increasing the handling time per order as items need to be passed between zones.
Batch picking, conversely, involves pickers potentially covering more ground to collect grouped items across multiple zones, but aims to minimize the total travel by intelligent grouping of items across all orders being processed.
When Should You Consider Using Batch Picking
If you've read this far and are currently wondering whether batch picking should be used for your picking operations, consider the following factors to determine if this method suits your needs:
High Volume of Small Orders
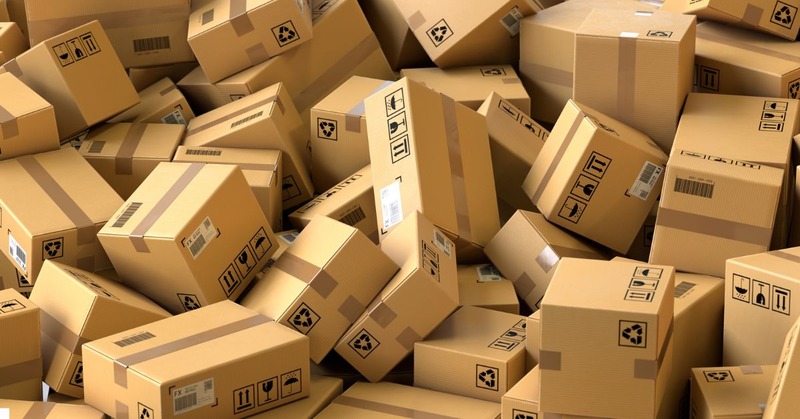
Batch picking is particularly beneficial in environments with a high volume of small orders that include similar items. This method consolidates picking tasks, reducing the time spent traveling between picks.
Common Items Across Orders
If your inventory data shows that many orders frequently include the same items, batch picking can significantly reduce picking time by allowing workers to pick these common items in bulk during a single pass through the warehouse.
Geographic Proximity of Inventory Items
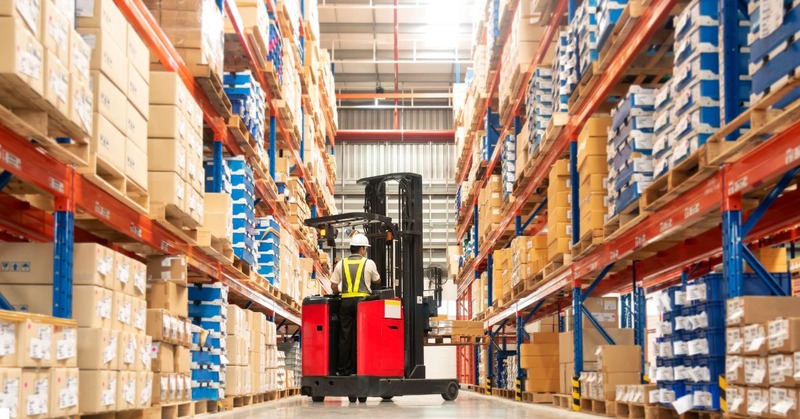
Batch picking is more effective when the items that frequently appear together in orders are stored near each other. If your warehouse layout supports or can be adjusted to accommodate this grouping, batch picking can maximize efficiency.
Flexible Shipping Times
If your operations can tolerate flexible shipping schedules, batch picking allows for the grouping of orders by shipping routes or delivery dates, optimizing logistics beyond the warehouse itself.
High Labor Costs
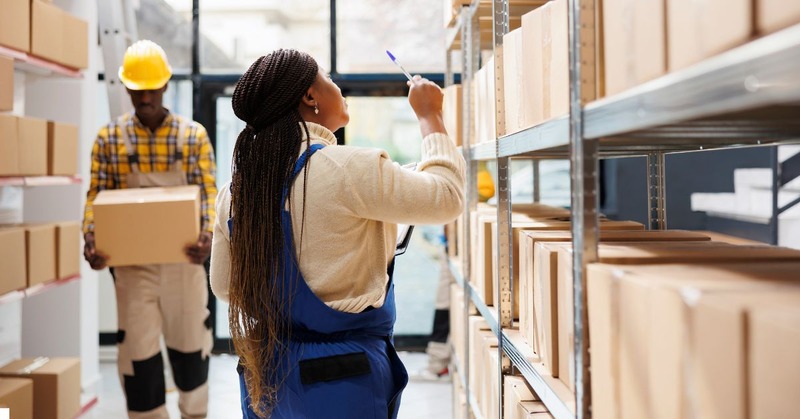
Implementing batch picking can reduce labor costs by minimizing the amount of time pickers spend walking and waiting. If labor costs are a significant concern, batch picking might offer substantial savings.
Technological Support
Having a robust Warehouse Management System (WMS) that can effectively generate optimized picking lists and manage inventory is crucial for batch picking.
Technology that supports batch optimization, like advanced sorting algorithms and real-time inventory updates, can make batch picking a feasible and highly efficient option.
Conclusion
Batch picking can significantly streamline your warehouse operations, but integrating it effectively requires the right tools.
Packiyo offers a robust warehouse management system (WMS) designed to enhance the efficiency of your picking processes.
With features like mobile smart picking, automated workflows, and real-time inventory tracking, Packiyo ensures that your batch picking operations are optimized for speed and accuracy.
If you want to read more topics such as this one, then consider reading through our blog where we’ll provide you with content such as ‘zone picking,’ ‘ecommerce warehousing,’ and more.
In conclusion, batch picking significantly reduces travel time within a warehouse, lowers the physical strain on workers, and increases overall productivity by allowing multiple orders to be fulfilled simultaneously.
We hope that we’ve helped you understand this topic a bit better now, and we’re looking forward to seeing you in our next article. Take care!
FAQs
Got more questions that you might have wondered as we went through the topic of 'batch picking'? Well, we might have answered some of them below!
What types of products are best suited for batch picking?
Batch picking is most effective for small to medium-sized products that are frequently ordered together.
It's particularly suited for items that are lightweight and easy to handle, which minimizes the physical strain on workers and speeds up the picking process.
Products that have similar storage requirements (e.g., temperature sensitivity) also benefit from batch picking, as they can be stored and picked from the same zones.
How does batch picking affect order accuracy?
Batch picking can improve order accuracy by reducing the number of transactions each picker must perform, which lowers the chance of error.
However, it relies heavily on accurate and up-to-date inventory data. Implementing quality checks at the sorting stage can further ensure accuracy before orders are shipped.
Can batch picking be integrated with automated systems?
Yes, batch picking can be seamlessly integrated with automated systems like conveyor belts, robotic pickers, and automated storage and retrieval systems (AS/RS).
These technologies can further optimize the batch picking process by speeding up item retrieval and reducing human error, making the system even more efficient.
What are the training requirements for implementing batch picking?
Training for batch picking generally involves familiarizing staff with the warehouse management system (WMS) and specific picking protocols.
Workers need to understand how to interpret pick lists, handle multiple orders simultaneously, and perform sorting tasks accurately.
Ongoing training is crucial as processes and technologies evolve.
How to measure the efficiency of batch picking?
The efficiency of batch picking can be measured by tracking metrics such as pick rates (items picked per hour), order accuracy rates, and the time taken from order receipt to shipment.
Comparing these metrics before and after implementing batch picking can provide insights into its impact on operational efficiency.