Looking to tighten up your supply chain and cut some costs? You might be considering something like milk run logistics—a nifty approach that could really streamline things if you juggle multiple suppliers.
In this guide, we'll talk about everything there is to know about milk runs, from what they are to how they work.
After reading, you'll be more likely to know whether this approach fits with your current needs or not.
Table of Contents
- What is a 'Milk Run' in Logistics?
- How is Milk Run Applied in Today’s Logistics?
- What are the Advantages and Disadvantages of Using Milk Run Logistics?
- Factors to Consider If You're Planning on Adopting Milk Run Logistics
- Conclusion
- FAQs
What is a 'Milk Run' in Logistics?
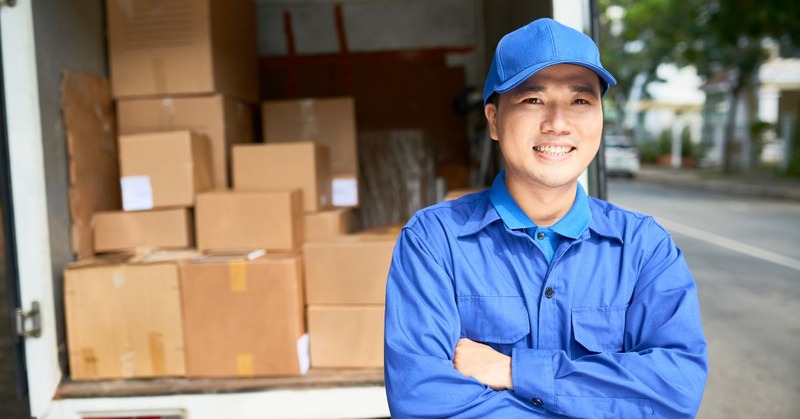
A "milk run" in logistics refers to a delivery system where a single vehicle collects and transports goods from multiple suppliers to a single destination, often on a recurring schedule to optimize the transportation process.
This method is particularly beneficial in settings that use just-in-time inventory management, as it ensures that only the necessary materials are replenished, reducing storage needs and minimizing waste.
History and Origins
This concept originates from the early 20th-century dairy industry, where it described the process of collecting milk from multiple dairy farms along a predetermined route.
This method was not only efficient but also helped in maintaining the freshness of the milk by ensuring daily deliveries.
The logistical approach of conducting 'milk runs' has since been adopted in various other industries to optimize supply chain operations by reducing transportation costs and improving delivery efficiency.
How is Milk Run Applied in Today’s Logistics?
The concept of "milk run" in logistics is effectively utilized in various industries to optimize transportation and inventory management.
Here are a few notable examples that illustrate its practical application:
Automobile Manufacturing
An automobile manufacturer might use a milk run to collect components from multiple suppliers.
A single truck follows a scheduled route to pick up items like steel, rubber, plastics, and other necessary parts from different suppliers located in close geographic proximity.
This approach supports just-in-time manufacturing by ensuring parts arrive exactly when needed, reducing the need for large storage spaces and minimizing overstock​.
Heavy Equipment Manufacturing
In settings like heavy equipment manufacturing facilities, milk runs are used internally.
Instead of each department delivering parts to the assembly area, a single driver collects all parts from various sections of the facility and transports them to the assembly area.
This method enhances efficiency and allows departments to focus on production rather than logistics​.
Amazon Warehousing
Amazon employs milk runs within its warehouses, where drivers move packages from one station to another to assist in sorting, packing, and loading operations.
This system helps maintain the flow of goods, especially for essential items like sanitization gear during high-demand periods​.
Retail and Supermarkets
Retail chains use milk runs to efficiently restock stores from distribution centers.
This method ensures that shelves are consistently replenished, improving inventory turnover and reducing the need for large backroom storage spaces​.
What are the Advantages and Disadvantages of Using Milk Run Logistics?
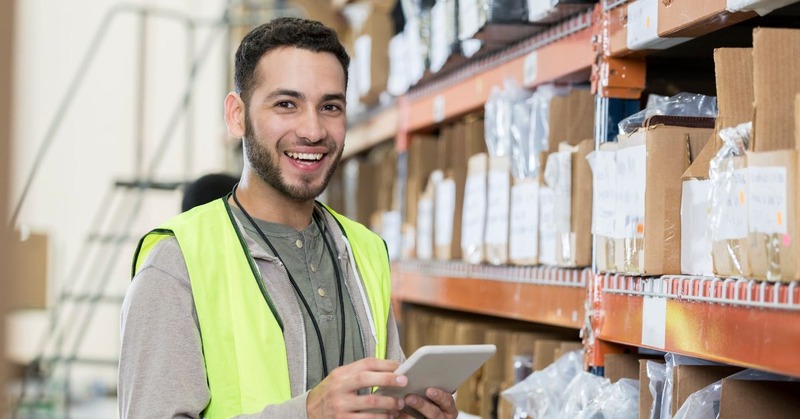
Now that we understand what milk runs are in general, let's take a look at how effective they are by examining their respective advantages and disadvantages:
Advantages
Efficiency and Cost Reduction
Milk runs consolidate multiple deliveries into one route, reducing the number of trips needed, which cuts down on fuel consumption and transportation costs.
Enhanced Supplier Relationships
Regular schedules enhance the coordination and cooperation between a business and its suppliers, which can lead to improved service and possibly better pricing or terms.
Support for Just-In-Time (JIT) Inventory
By receiving goods only as needed, companies can significantly reduce the need for large storage spaces and lower the capital tied up in unused inventory.
Disadvantages
Complexity in Planning and Coordination
Implementing a milk run requires meticulous route and schedule planning. Any disruption, such as a supplier failing to meet their shipment schedule, can impact the entire supply chain.
Limited Flexibility for Unscheduled Needs
While regular schedules offer many benefits, they can also make it difficult to respond swiftly to unexpected changes in demand or supply issues.
Investment in Technology and Equipment
Effective milk runs may require sophisticated logistics technology and equipment to coordinate and track movements, which can be a significant upfront cost.Â
Factors to Consider If You're Planning on Adopting Milk Run Logistics

Before adopting milk run logistics, it's important to carefully consider various aspects that could influence its effectiveness.
That's why in this section, we'll highlight the important factors that you need to consider to determine whether this approach suits your logistical needs.
Supplier Coordination and Commitment
Supplier Buy-In
Ensure that all involved suppliers are committed to the milk run schedule. This includes their agreement on timing, pickup points, and the ability to consistently meet these commitments.
Coordination Complexity
Assess the number of suppliers, their geographic locations, and their ability to adhere to strict delivery windows, as coordination increases with more suppliers and dispersed locations.
Route and Schedule Optimization
Route Planning
Develop efficient routing to minimize travel time and costs. This includes considering traffic patterns, distance between stops, and vehicle capacity.
Schedule Consistency
Maintain consistent scheduling to support just-in-time inventory practices, ensuring that parts or materials arrive precisely when needed without excess inventory buildup.
Cost Analysis
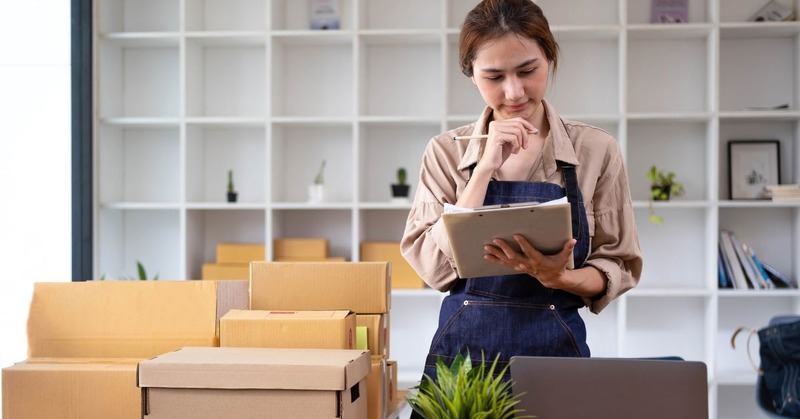
Initial and Ongoing Costs
Evaluate the upfront investment for setting up milk run logistics and the ongoing costs of operation. This includes potential savings from reduced inventory holding costs against the expenses of additional planning and technology.
Return on Investment (ROI)Â
Calculate the expected return on investment from implementing milk run logistics by analyzing cost savings from reduced transportation and warehousing needs.
Technology and Infrastructure
Technology Needs
Identify the necessary technology for tracking and managing the milk run effectively, such as transportation management systems (TMS) and real-time GPS tracking.
Infrastructure Suitability
Ensure that both your infrastructure and that of your suppliers can support milk run operations, including appropriate loading docks and storage facilities.
Risk Management
Disruption Risks
Plan for potential disruptions in the supply chain, such as supplier failures or transportation delays, and develop contingency plans.
Flexibility and Scalability
Consider whether the milk run model allows for flexibility in case of demand fluctuations or business scale-up.
Environmental Impact
Sustainability Benefits
Evaluate the environmental benefits of adopting milk run logistics, such as reduced carbon emissions from fewer trips and the opportunity for more sustainable operations.
Legal and Compliance Issues
Regulatory Compliance
Check all relevant transport and industry regulations to ensure that your milk run logistics plan complies with local, national, and international laws.
Contractual Agreements
Set up clear contractual agreements with all parties involved to outline responsibilities, liability, and conflict resolution mechanisms.
These factors provide a comprehensive checklist for businesses considering milk run logistics, helping to ensure a thorough evaluation of its potential benefits and challenges.
Conclusion
So to end things, milk run logistics offer a streamlined approach to managing supply chains, significantly reducing costs and improving efficiency. By ensuring just-in-time delivery, this strategy minimizes waste and optimizes operations.
Integrating Packiyo enhances these benefits further.
Its robust features like inventory management, seamless order processing, and automation ensure operations are not just efficient but also accurate.
With Packiyo, you can manage your logistics across multiple suppliers more easily by ensuring that your operations can adapt quickly to changes without compromising on quality.
Read more about us on our blog, where we cover topics like 'What is Discreet Shipping?' and 'What is a Shipping Carrier?'. If you have any questions, don't hesitate to contact us; we'll be more than happy to assist you with your needs.
Understanding what milk run is and how it works is something that you can leverage in your operations, and we're happy that we've helped you with that end!
FAQs
Got more questions about milk runs? Maybe we've answered them below!
What industries benefit most from implementing milk run logistics? Milk run logistics are particularly beneficial in industries with high-volume, predictable demand and numerous local suppliers, such as automotive, electronics, and manufacturing. These sectors can leverage milk runs to streamline supply chains and reduce inventory costs.
Can milk run logistics be used for international shipments? While traditionally used for local or regional deliveries, milk run logistics can be adapted for international use if suppliers and delivery points are strategically located. The key is effective route planning and scheduling to handle cross-border complexities such as customs and varying transport regulations.
What technologies enhance the efficiency of milk run logistics? Technologies such as GPS for real-time tracking, RFID for inventory management, and advanced transportation management systems (TMS) are crucial. They help in route optimization, real-time updates, and efficient management of the logistics process.
How do businesses handle the increased complexity of scheduling in milk runs? Companies often use sophisticated software tools for route planning and optimization. These tools consider various factors like traffic conditions, delivery windows, and vehicle capacity to create efficient schedules.
What are the typical challenges when transitioning to milk run logistics from traditional logistics models? Challenges may include initial setup costs, the need for collaboration and synchronization between multiple suppliers, and the potential resistance to change from established logistics patterns. Effective communication and gradual implementation can help overcome these obstacles.
How do companies measure the success of milk run logistics? Success can be measured through key performance indicators such as reduction in transportation costs, improvement in delivery times, decrease in carbon footprint, and enhanced supplier relationships.
Can milk run logistics be combined with other supply chain strategies? Yes, milk run logistics can be effectively combined with strategies like just-in-time (JIT) inventory and lean manufacturing to further optimize supply chain efficiency and reduce waste.