Consider a large tool shed filled with an assortment of items, from power tools to hand tools, garden supplies, and kitchen utensils.Â
Now, suppose a friend asks you for a specific set of items from that shed: a hammer, a chef's knife, and a garden trowel. To fulfill your friend's request, you would go into the shed, search for those specific items, and then retrieve them to give to your friend.Â
This process of locating and gathering the items your friend asked for closely mirrors what is known as 'order picking' in a warehouse or store setting. If you're here to understand what this term means, then you're in the right place.
In this guide, you'll learn what order picking is, its advantages, different types, and additional topics that will get you up to date with everything you need to know about it.
With that said, let's get started.
Table of Contents
- What is Order Picking?
- What are the Different Types of Order Picking Systems?
- Tips When Choosing Your Order Picking System
- Conclusion
- FAQs
What is Order Picking?
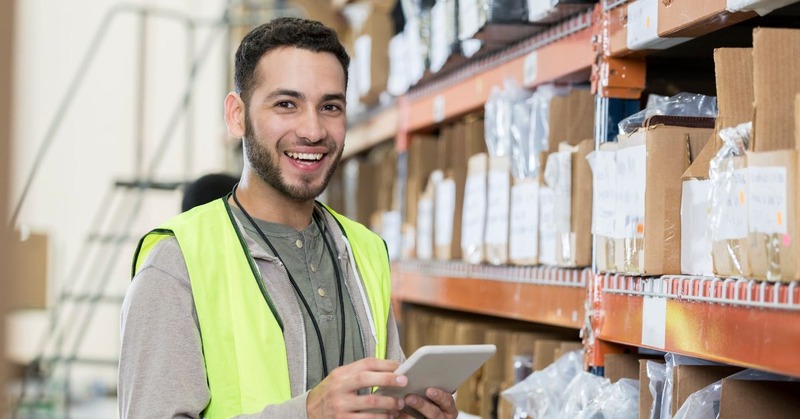
Order picking involves selecting and collecting items from a warehouse to complete customer orders, a crucial step in the supply chain.
This process is essential for businesses that handle inventory and deliveries as it ensures customers receive the correct products promptly, directly impacting satisfaction.
Building on our tool shed story, think of order picking as looking for certain tools in a big shed to satisfy a friend's need. Warehouse workers do something similar, finding specific items in a large inventory to complete orders fast and right.Â
Just like getting the right tools makes your friend happy, doing this job well keeps customers satisfied.
Why is Order Picking Important?
Order picking plays a vital role in the fulfillment process, directly impacting customer satisfaction, operational efficiency, and the overall success of businesses involved in storing and shipping goods.
Here are the top three benefits that underscore its importance:
Reduces Warehouse Costs
Efficient order picking reduces labor and operational costs by optimizing pickers' routes and minimizing manual error through automated picking lists. This efficiency cuts down on time spent per order, directly lowering warehouse expenses.
Improves Customer Satisfaction
Quick and accurate order picking boosts customer satisfaction by ensuring timely delivery of correct orders. This efficiency leads to fewer complaints and returns, increasing customer loyalty and the likelihood of repeat purchases.
Makes Pickers’ Jobs Easier
An optimized picking system streamlines the picking process, reducing human error and physical strain. By guiding pickers with clear routes and visual validations, it enhances job satisfaction and overall productivity in fulfilling orders.
What are the Different Types of Order Picking Systems?
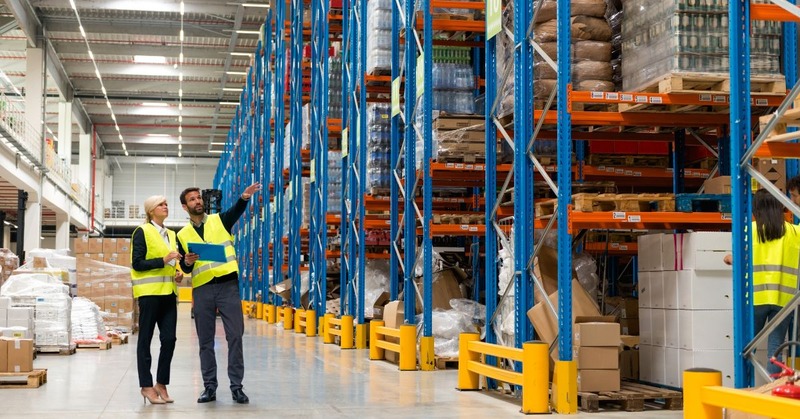
Understanding various order picking strategies is essential for optimizing warehouse operations. Each method has its advantages and challenges, impacting efficiency, cost, and customer satisfaction.
Below, we'll explore several popular order picking types along with their pros and cons.
Piece Picking / Pick and Pack
Piece picking, also known as "pick and pack," involves workers picking individual items to fulfill each order one at a time.
Pros
- Suitable for a wide range of orders, especially those requiring a mix of different items.
- It's most effective for small businesses or those with a low volume of orders
- High level of order accuracy since items are picked individually.
Cons
- Picking items individually can be slower than other methods.
- Requires more manpower, increasing operational costs.
Pallet Picking
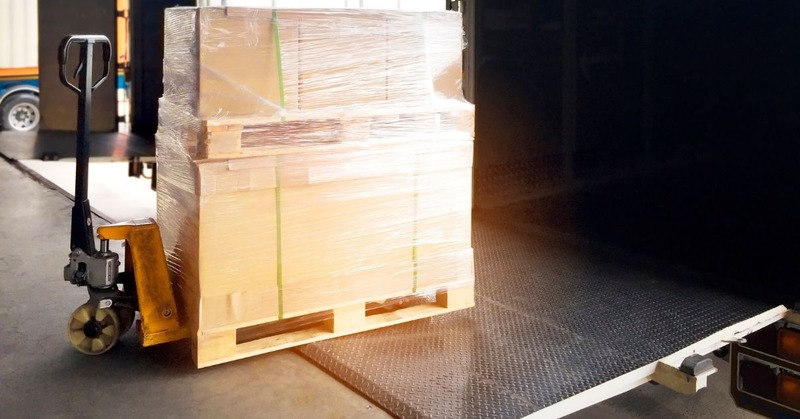
Selecting and moving an entire pallet of items, which can consist of one large item or several smaller ones.
Pros
- Moving entire pallets is fast and efficient for large quantities of the same item.
- Reduces labor costs for bulk orders.
Cons
- Not suitable for orders requiring a mix of items.
- Requires forklifts or pallet jacks, limiting its use to facilities equipped for such handling.
Case Picking
Picking a portion of a pallet, used for a large number of SKUs with fewer items per SKU.
Pros
- Good for orders that need more than one item but less than a full pallet.
- Strikes a balance between piece picking and pallet picking in terms of efficiency and flexibility.
Cons
- More complex to manage than pallet picking, as it may require breaking down pallets.
- Can be physically demanding, as workers may need to lift and move heavy cases.
Single Order Picking
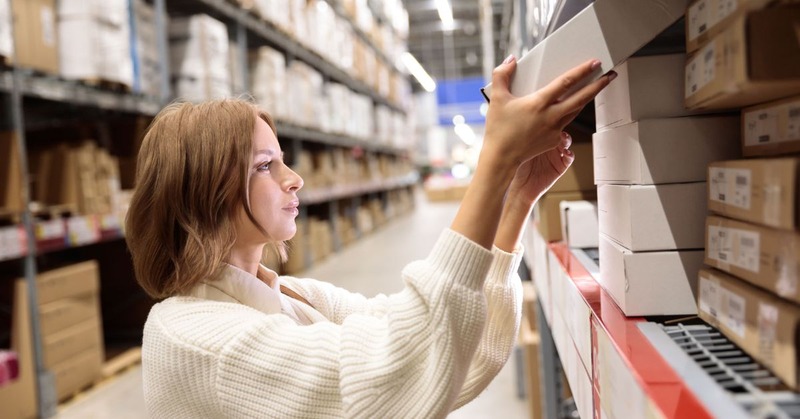
Picking one order at a time, typically in smaller warehouses with low traffic.
Pros
- High accuracy since focus is on one order at a time.
- Simplifies tracking and management of orders.
Cons
- Time-consuming due to repeated trips for different orders.
- Not suitable for high-volume environments.
Batch Picking
Handling multiple orders in one go, ideal for many orders with a small number of products each.
Pros
- Reduces travel time by picking multiple orders in one go.
- Efficient for orders sharing common SKUs.
Cons
- Requires careful planning to organize orders effectively.
- Potential for increased picking errors with more complex orders.
Zone Picking
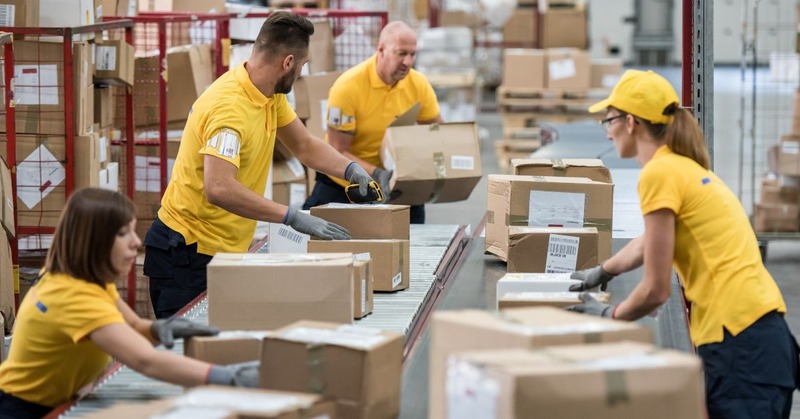
Assigning pickers to specific zones, beneficial for high-volume orders.
Pros
- Enhances picking efficiency by dividing warehouse into zones.
- Allows specialization of workers in specific areas, improving speed and accuracy.
Cons
- May require advanced warehouse management systems for coordination.
- Less flexible in handling sudden changes in order volume or SKU location.
Pick-and-Pass
Passing an order through zones until all items are picked, usable with all types of picking processes.
Pros
- Sequential movement through zones speeds up picking.
- Distributes tasks evenly across zones.
Cons
- Needs advanced tracking and management.
- Disruptions in one zone can halt the process.
Wave Picking
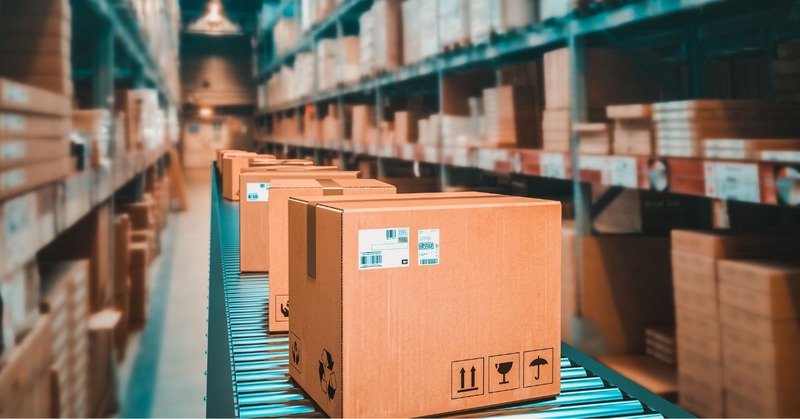
Simultaneous item selection from different zones for order consolidation, aimed at quick shipping of high-volume orders.
Pros
- Combines the benefits of batch and zone picking for high efficiency.
- Scheduled picking times optimize workflow and shipping operations.
Cons
- Complex to plan and execute, needing sophisticated software.
- Might not be as effective in warehouses with a limited number of SKUs.
Cluster Order Picking
Completing multiple orders at once by gathering multiple items from different locations simultaneously.
Pros
- Allows picking of multiple orders simultaneously with varied SKUs.
- Reduces travel time and improves order throughput.
Cons
- Requires equipment like picking carts, which may increase upfront costs.
- Can be challenging to manage without proper order management systems.
Sorting System
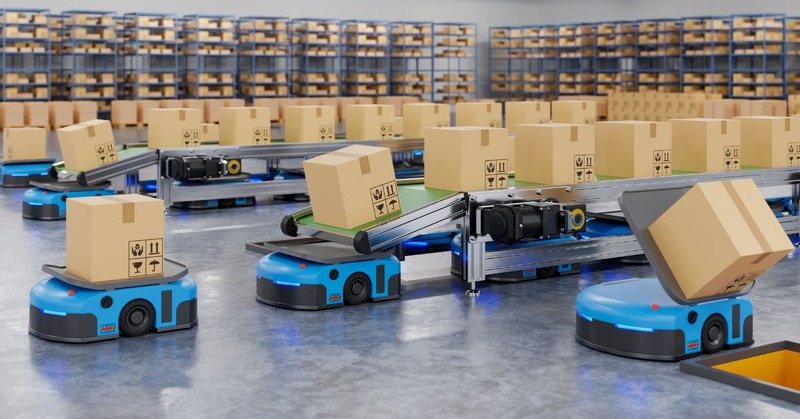
Using conveyor belts and automation for sorting items, enhancing efficiency and automation in the picking process.
Pros
- Automated sorting increases throughput.Â
- Reduces human error in order sorting.
Cons
- High initial investment in technology.
- Requires regular upkeep and technical support.
Pick to Box System
Placing a box on a conveyor belt which moves through zones to be filled, suitable for handling large volumes of orders.
Pros
- Streamlines order assembly by moving boxes to items.
- Handles large order volumes efficiently.
Cons
- Requires space for conveyor systems.Â
- Can be complex to implement and manage.
Picker to Part System
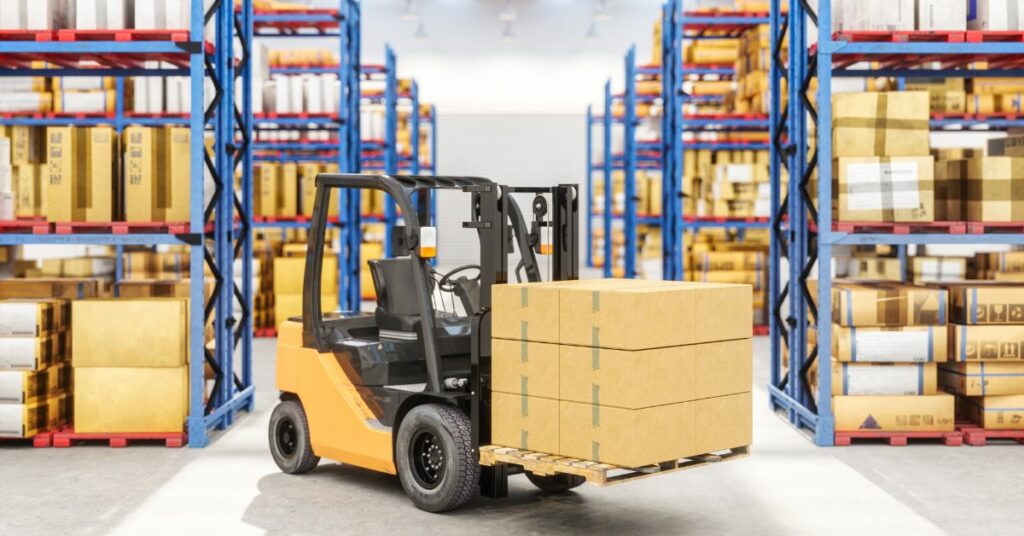
A material handling area is set up for forklifts to transport inventory to a picking area for order assembly.
Pros
- Adaptable to various inventory sizes and types.
- Reduces picker movement, speeding up the picking process.
Cons
- Relies on forklifts and material handling equipment.
- Requires skilled operators for equipment.
Part to Picker System
Order pickers wait in picking bays for items to be delivered from the material handling area, suitable for flexible workflows but may increase travel time.
Pros
- Minimizes picker movement for faster order fulfillment.
- Decreases physical strain on workers.
Cons
- Needs investment in automation and conveyor systems.
- Requires advanced systems for coordinating item delivery to pickers.
Tips When Choosing Your Order Picking System

When it comes down to ramping up the efficiency of your warehouse operations, picking the right order picking system is more than just a necessity—it's a game changer.Â
Let’s dive into some insights on how to make that all-important choice.
Assess Your Warehouse Size and Inventory
The size and complexity of your warehouse and inventory play a pivotal role in determining the most suitable picking system. For sprawling warehouses, zone or batch picking systems can streamline operations by dividing the space into manageable sections or grouping similar orders.
On the flip side, smaller spaces often benefit from the simplicity and directness of single order or piece picking methods. The key here is to match the system not just to your current layout and inventory but to anticipate future growth and changes.
Consider Your Workforce
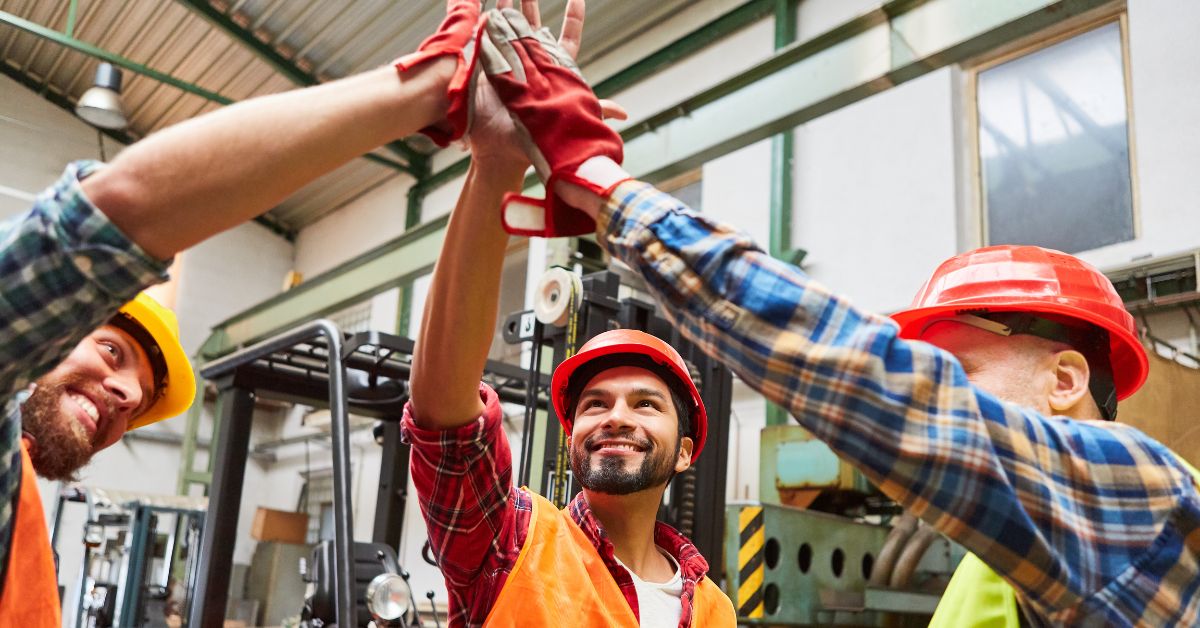
The efficiency of your picking system is as good as the team behind it. Larger teams might find zone picking advantageous as it allows pickers to become experts in their area, reducing congestion and improving speed.
However, this requires a thoughtful approach to training and assigning roles based on skill levels and ergonomic considerations. It’s about finding that sweet spot where the system supports your team’s strengths and minimizes their workload.
Leverage Technology
In today's tech-driven world, integrating a Warehouse Management System (WMS) can transform your picking process. By guiding pickers through the most efficient routes and keeping real-time tabs on inventory levels, a WMS can significantly cut down on wasted time and errors.
Automation, too, is not just a buzzword but a practical tool. From conveyor belts to robots, these solutions can speed up the picking process, albeit with an eye on the required investment in skills and maintenance.
Optimize Warehouse Layout and Equipment
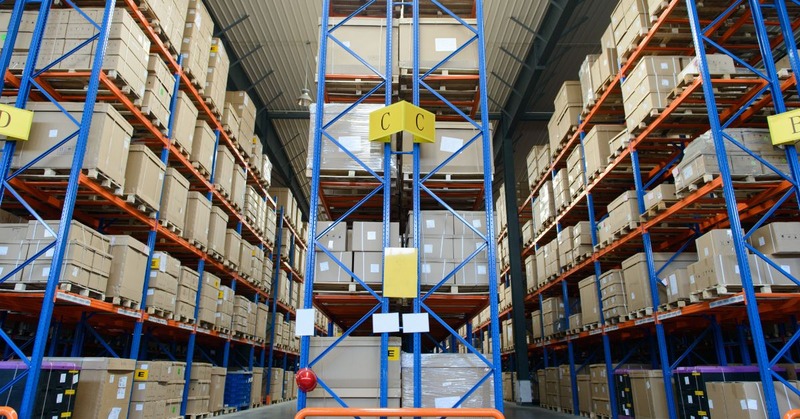
Optimizing your warehouse layout to minimize travel time and ensuring that frequently picked items are easily accessible can significantly boost picking efficiency.
This involves not just a smart arrangement of inventory but also investing in the right equipment. Whether it’s forklifts for pallet picking or barcode scanners for piece picking, the right tools can make a big difference in operational speed and safety.
Analyze Your Data
Data analysis isn’t just for the tech-savvy. Understanding the patterns in your orders—like average size, frequency, and complexity—can provide invaluable insights into which picking system will best suit your needs.
Moreover, keeping a close eye on performance metrics will help you identify areas for improvement, ensuring your system evolves along with your business.
Safety and Ergonomics
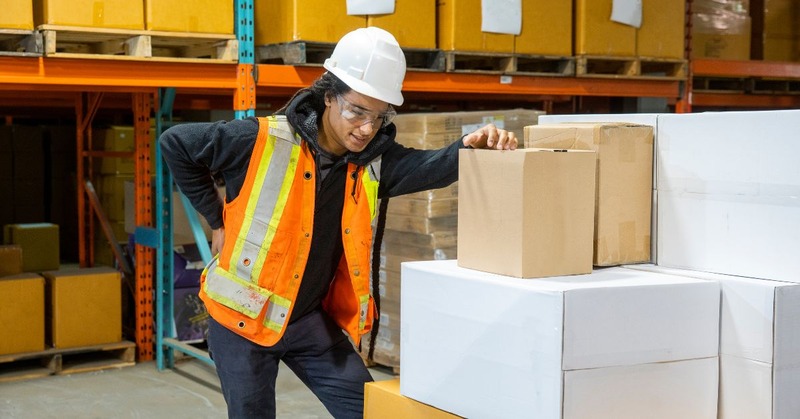
Never underestimate the importance of safety and ergonomics. A picking system that prioritizes the well-being of your workers not only minimizes the risk of injuries but also boosts overall satisfaction and efficiency.
Regular training on safe practices and ergonomic techniques is essential, ensuring everyone is up to speed and comfortable with your chosen system.
Combining Systems
Don’t be afraid to mix and match. Sometimes the best approach is a hybrid one, combining elements of different picking systems to best meet the unique demands of your operation. Flexibility is key, allowing your system to adapt to changes in order volume, seasonal peaks, and inventory shifts.
Set Clear Goals
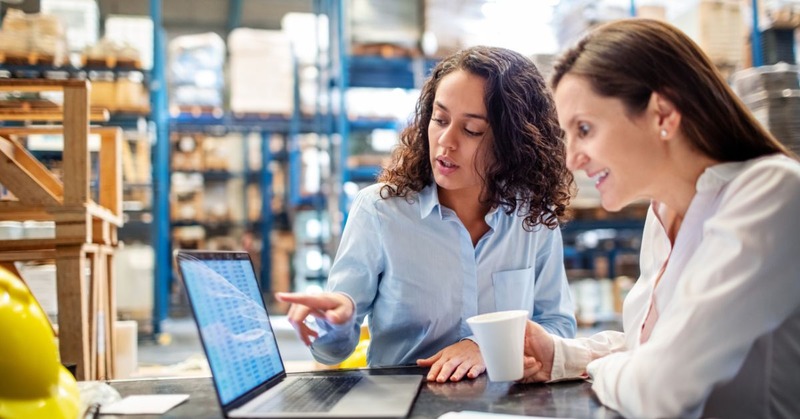
Last but not least, setting clear, achievable goals for your picking operations is crucial. Aim for a balance between productivity and accuracy, ensuring your system not only moves goods quickly but also correctly. Efficient use of space and resources should guide your strategy, keeping your operations lean and agile.
Conclusion
For both eCommerce businesses and 3PL providers, Packiyo uses smart inventory management to ensure every order is handled perfectly from start to finish.
Our advanced warehouse management tools make your order picking faster and more accurate.
If you're interested in availing yourself of our services, consider checking out our pricing. If you want to explore more topics similar to this one, head over to our blog where we tackle topics such as order picking, case picking, pick and pack, and more.
In conclusion, choosing the right order picking system is a blend of art and science, requiring a deep understanding of your operations and a forward-looking approach.
By keeping these tips in mind, you'll be well on your way to optimizing your warehouse for peak performance.
We hope you've learned something new today, and we look forward to seeing you in the rest of our articles.
FAQs
What are the common challenges with order picking? Common challenges with order picking include maintaining high accuracy and speed, managing the physical and logistical constraints of warehouse layouts, and dealing with variability in order volume and inventory. Overcoming these challenges often requires strategic planning, technological integration, and continuous process improvement.
How do you measure the efficiency of your order picking process? Measuring the efficiency of an order picking process typically involves tracking key performance indicators (KPIs) such as pick accuracy, pick time, and order fulfillment rate. Efficiency is assessed by the speed and accuracy with which orders are completed, alongside the cost implications of the picking process.
Can you combine warehouse picking strategies? Yes, you can combine warehouse picking strategies to enhance efficiency and adaptability. This approach allows for leveraging the strengths of various methods to suit different types of inventory, order sizes, and warehouse layouts.
For example, zone picking can be combined with batch picking to handle multiple orders efficiently within designated areas of the warehouse, reducing travel time and increasing throughput. Similarly, wave picking can be used alongside discrete picking for prioritizing urgent orders while efficiently managing regular orders.
What's the difference between order picking and an automated picking system?
Order picking involves manually selecting items from a warehouse to fulfill orders, relying on human labor and potentially semi-automated tools. In contrast, an automated picking system uses technology, such as robots or conveyor belts, to select and move items with minimal human intervention, aiming to increase efficiency and accuracy in the fulfillment process.