If you're feeling overwhelmed by the chaos of your warehouse during peak order times, then you're definitely not alone.
Many warehouse managers and business owners like yourself face this challenge of ensuring that every order is accurate, timely, and fulfilled.
In this article, we'll guide you through what a pick list is, how it can improve your current workflow, and how this simple yet powerful tool can transform your warehouse operations from hectic to harmonious.
If you're still here reading, then let's pick up the pace and get started!
What is a Pick List?
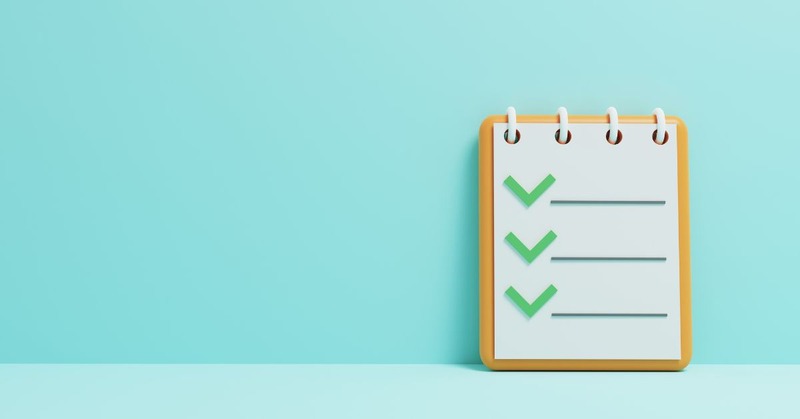
A pick list is a document or digital tool used primarily in warehouse operations to streamline the process of gathering items from inventory to fulfill customer orders. It acts as a guide for warehouse staff, detailing which items need to be picked and where they are located.
How It Works
The functioning of a pick list begins with the preparation phase, where the required items for orders are listed based on customer requests.
This list is then used by warehouse staff to physically collect the items from their storage locations.
1. Creation
A pick list is created either manually or via systems like OMS or WMS, detailing items required for incoming orders.
2. Distribution
The pick list is given to warehouse staff, possibly through digital devices that allow for real-time updates.
3. Picking Process
Staff use the pick list to efficiently collect items from designated warehouse areas, often following strategies like zone or wave picking to reduce travel time.
4. Verification and Updates
Items are checked against the pick list for accuracy, with discrepancies corrected and updates made via barcode or RFID scanning.
5. Final Steps
After verification, items are packed and prepared for shipment, with system updates marking the completion of the order.
Types
Physical Pick Lists
Physical pick lists are traditional paper lists used by warehouse pickers to collect items. They are cost-effective and simple to use but can be inefficient as they don't allow real-time updates and are prone to human error.
Digital Pick Lists
Digital pick lists are operated on mobile devices or tablets and are connected to a Warehouse Management System (WMS). This integration enhances accuracy, speeds up the fulfillment process, and is ideal for managing large-scale operations.
They enable real-time tracking of inventory and orders, support barcode scanning for accuracy, and facilitate quick adjustments to warehouse activities.
What Are the Key Elements Within a Pick List?
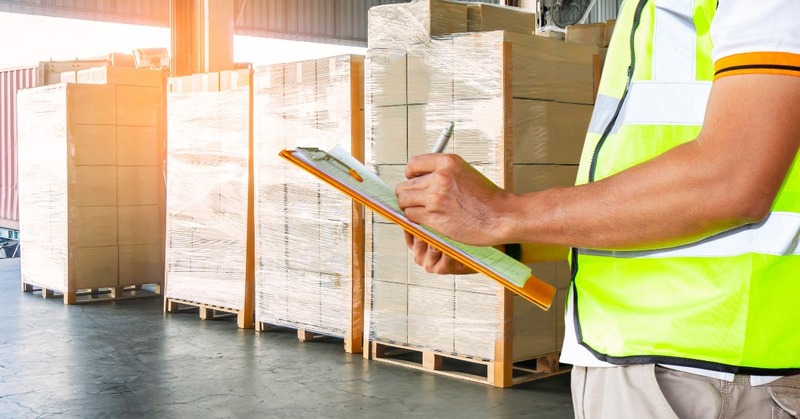
If you want to know what a pick list typically includes, here's a breakdown:
Product Information
This typically includes product descriptions, SKU numbers, and possibly barcodes or UPC codes. For certain products, such as those with variations like size or color, the SKU will specify the exact variant needed.
Quantity
Each item on the pick list will have a specified quantity that needs to be picked.
Order Details
Important details like the order number and the date and time the order was placed are included to prioritize the picking process, especially under tight shipping deadlines.
Location Details
To streamline the picking process, the location of each item within the warehouse is specified. This can be a physical location like a specific aisle and shelf or a bin number.
Additional Information
Depending on the complexity of the items and the warehouse system, additional details like pictures of the items, unit size, and weight may also be included to help pickers identify the correct items quickly and prepare the necessary equipment for handling.
Now that you understand what a typical pick list consists of, let's go through the next section where you'll try making your own pick list.
How to Create Your Own Picking List

Creating a pick list for warehouse operations involves several steps to ensure accuracy and efficiency in fulfilling orders.
Here’s a step-by-step guide to creating an effective pick list:
Choose the Type of Pick List
Decide whether to use a physical or digital pick list. Physical pick lists are traditional and involve paper lists, while digital pick lists utilize devices like tablets and are connected to a Warehouse Management System (WMS) for real-time updates and inventory tracking.
Gather Essential Information
Include key details such as order number, product SKUs or UPC codes, product descriptions, quantities, and specific warehouse locations (aisle, shelf, bin). This information helps pickers locate and verify the correct items efficiently.
Add Date and Time of Order
Including the date and time the order was placed helps prioritize orders based on delivery requirements, such as same-day or two-day shipping demands.
Utilize Product Details
Provide detailed descriptions or photos of the items, especially for products that are similar in appearance, to prevent picking errors. Barcodes can also be included to allow for quick scanning and verification.
Organize Items Logically
Arrange items on the pick list in a way that minimizes travel time within the warehouse. This can be achieved through methods like zone picking, where items are grouped by their physical locations, or batch picking, where similar orders are picked simultaneously.
Implement a Warehouse Management System (WMS)
A WMS can automate the creation of pick lists and provide real-time data on inventory levels, which helps in maintaining accuracy and reducing manual errors. It can also track picker progress and update inventory automatically.
Review and Optimize
Regularly review the picking process and pick list format to find areas for improvement, such as adjusting the layout or updating technology used. This continuous improvement will help in adapting to changes in order volume and operational demands.
By following these steps, you can create a pick list that enhances the efficiency of your warehouse operations, reduces errors, and improves overall customer satisfaction.
Related Questions
What are the common challenges in using pick lists in warehouse operations?
Common challenges include managing outdated information, dealing with inaccuracies in inventory data, navigating inefficient item locations that increase picking time, and handling changes in order volumes which can outpace the current system's capabilities.
What training do warehouse staff need to effectively use pick lists?
Staff should be trained on interpreting pick list information correctly, using any associated technology (like scanners or tablets), and understanding the warehouse layout. Training often includes handling special cases, such as items that require specific picking techniques or equipment due to size or weight.
READ MORE: What is Warehouse Maintenance?
How are pick lists customized for different types of warehouses?
Pick lists can be customized by the layout and operations of a warehouse. For instance, a warehouse that uses high-volume automated picking might use zone or wave picking strategies reflected in their pick lists, while a smaller facility might use simpler, manual batch picking lists.
How often should pick lists be updated to reflect changes in inventory and operations?
The frequency of updates depends on the volume of orders and the dynamics of inventory. High-turnover environments might require real-time updates facilitated by a WMS, whereas less dynamic settings might update lists daily or weekly.
What are the best practices for creating a pick list that minimizes picking errors?
Best practices include using clear, concise descriptions, including precise location details, employing barcodes for easy scanning, and designing the list layout to reflect the physical layout of the warehouse to minimize travel time.
Final Thoughts
In conclusion, understanding the utility of a pick list in warehouse operations highlights the need for efficiency and accuracy in order management.
Packiyo's WMS provides an advanced solution for these needs by facilitating the digital management of pick lists, which enhances the speed and accuracy of the picking process.
Features such as Mobile Smart Pick and Co-Pilot can further optimize your current picking process while also guiding your warehouse pickers in real-time. This ensures a faster and more accurate order fulfillment.
For businesses looking to optimize their warehouse operations, Packiyo offers a powerful tool that adapts to modern logistical demands, making it an ideal choice for improving overall operational efficiency.
Read more through our blog with topics like 'warehouse maintenance checklist', 'delayed shipping', and more. Alternatively, contact us directly if you have any questions about creating your pick list—we'll be more than happy to help you with what you need.
With that said, we hope we've been helpful on this topic, and we look forward to seeing you in our next article!