In the fast-paced world of e-commerce, getting orders to customers quickly and accurately is crucial. If you've faced delays, misplaced items, or high shipping costs, you're not alone.
The pick, pack, and ship process can help streamline your operations, reduce errors, and improve customer satisfaction.
This guide will explore each stage, highlight the benefits and potential downsides, and help you decide if it's right for your business.
Table of Contents
- What is âPick, Pack, and Shipâ?
- How Does the Process of Picking, Packing, and Shipping Work?
- How to Know if the Pick, Pack, and Ship Process Meets My Warehousing Needs
- FAQs
- Conclusion
What is âPick, Pack, and Shipâ?
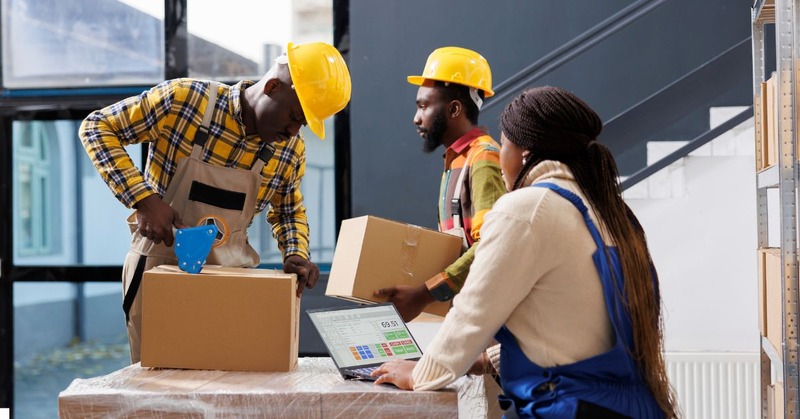
The pick, pack, and ship process is a streamlined method used in warehouses to efficiently fulfill customer orders.
It involves three main stages: picking, where items for an order are retrieved from their storage locations; packing, where the items are securely packed into boxes; and shipping, where the packages are labeled and dispatched to the customer.
How Does the Process of Picking, Packing, and Shipping Work?
For example, imagine an online bookstore receiving an order for three different books. The warehouse team would first pick the books from their respective shelves, pack them into a single box with protective materials to prevent damage, and then ship the box using the best carrier option to ensure it arrives promptly.
This process helps businesses reduce errors, improve efficiency, and meet customer expectations for fast and reliable service.
Here's the step-by-step process in more detail:
Picking Stage

The picking stage is the first and crucial step in the fulfillment process, where items are selected from inventory to fulfill customer orders. Here's how it typically works:
Piece Picking
This method involves picking individual items as orders come in, similar to shopping at a grocery store. It's straightforward but can be inefficient for larger volumes.
Batch Picking
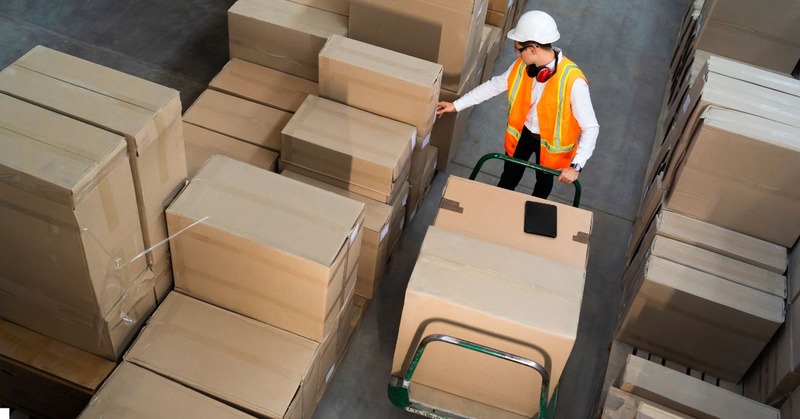
Multiple orders are picked at the same time, reducing travel time across the warehouse, which enhances efficiency.
Zone Picking
The warehouse is divided into zones, and pickers are assigned to specific areas. This method speeds up the picking process and reduces errors.
Wave Picking
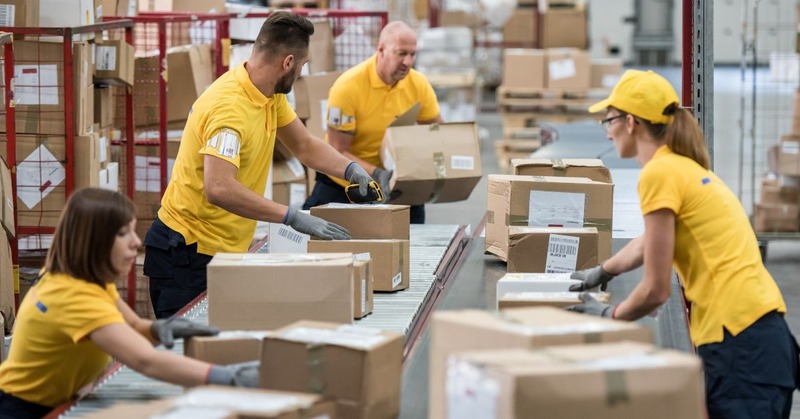
A combination of batch and zone picking where items for multiple orders are picked at scheduled intervals.
ALSO READ: Whatâs the Difference Between Batch Picking and Wave Picking?
Packing Stage
Once items are picked, they move to the packing stage. Effective packing ensures that items reach customers safely and cost-effectively:
Selection of Packing Materials
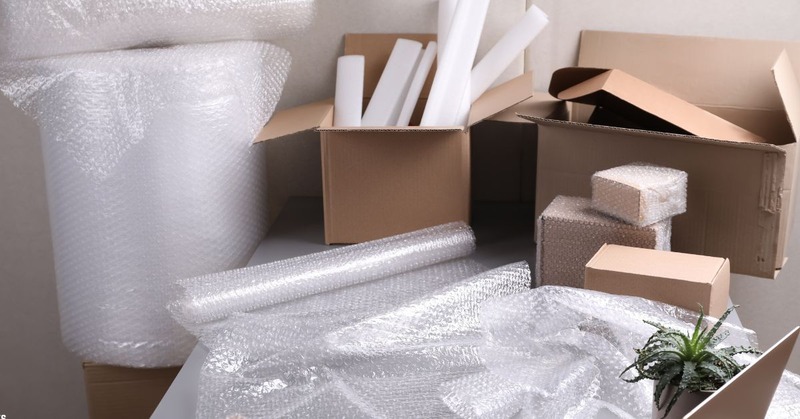
Based on the item's size, weight, and fragility, appropriate packing materials are chosen, such as bubble wrap or packing peanuts, to protect items during transit.
Packing Strategy
Implementing box-sizing algorithms can help minimize shipping costs and material waste. Each order is carefully packed, sometimes using custom packaging to enhance the customer experience.
Quality Control
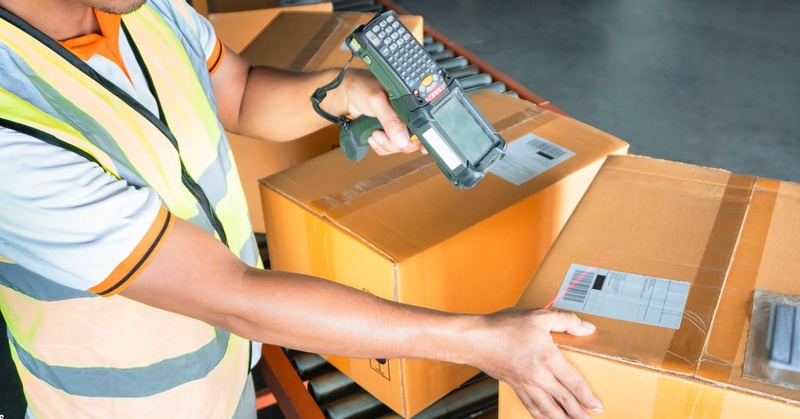
Ensures the correct items are packed and meet quality standards. Packing slips and barcodes are often used to track and verify orders.
Shipping Stage
The final stage involves getting the order to the customer:
Carrier Selection
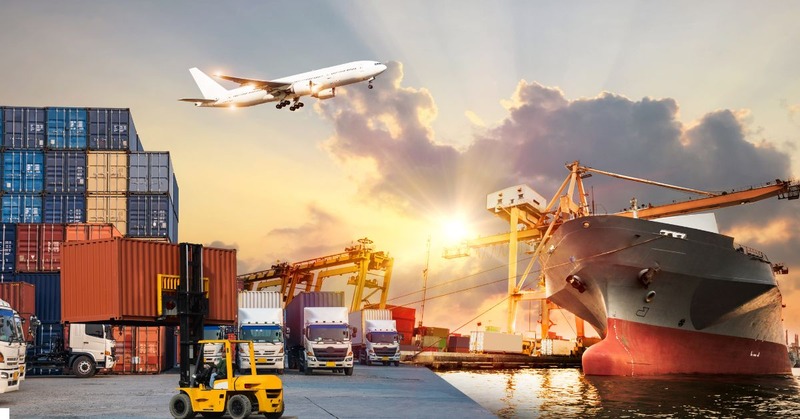
Depending on factors like delivery speed required and shipping costs, an appropriate carrier is chosen.
Order Consolidation
Orders destined for similar locations may be consolidated to reduce shipping costs.
Tracking and Updates
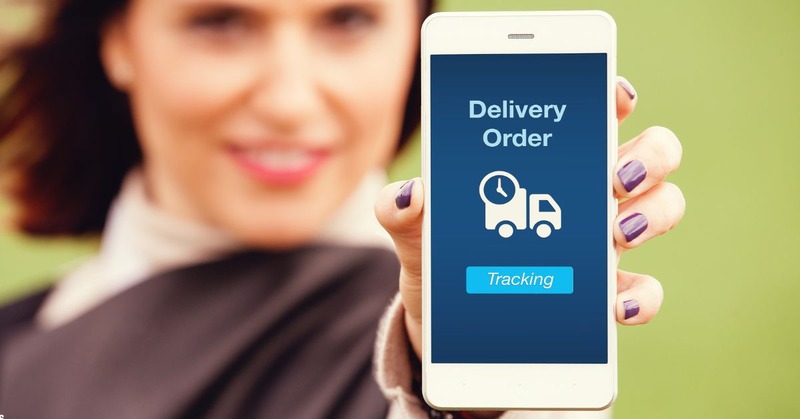
Once shipped, orders are tracked, and customers are kept updated on the status of their delivery.
Each stage is interconnected and optimized with technology and strategic planning to ensure efficiency and customer satisfaction. This approach streamlines operations and supports business growth and scalability.
What are the Benefits and Potential Downsides to the Pick, Pack, and Ship Process
Let's explore the pros and cons of this process to dissect it further:
Benefits
The pick, pack, and ship process offers several advantages that can significantly enhance business operations:
Improved Efficiency and Productivity
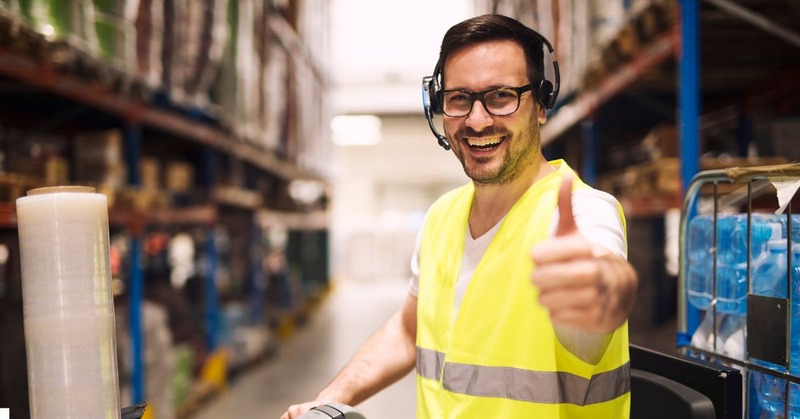
By streamlining the picking, packing, and shipping steps, businesses can optimize workflows and reduce the time and effort involved in fulfilling orders. This efficiency is achieved by minimizing unnecessary movement and organizing inventory in a logical manner.
Enhanced Customer Satisfaction
Timely and accurate order fulfillment strengthens customer loyalty and helps businesses stand out from competitors. A well-executed pick, pack, and ship process ensures that customers receive the correct products without errors or delays, which is crucial for building trust and repeat business.
Cost-Effectiveness
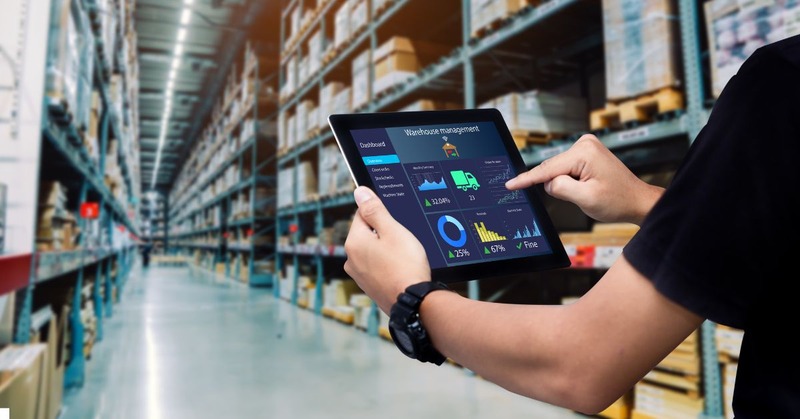
Integrating picking and packing with warehouse management systems (WMS) can automate tasks and prioritize orders, thus reducing labor costs and improving the return on investment. Additionally, the use of collaborative robots in these processes can further increase precision and speed, contributing to overall cost savings.
Scalability
The pick, pack, and ship process is adaptable to varying order volumes and business growth. This scalability allows businesses to handle increased demand without a significant increase in errors or delays.
Potential Downsides
However, there are also some potential downsides to consider:
Complexity in Implementation
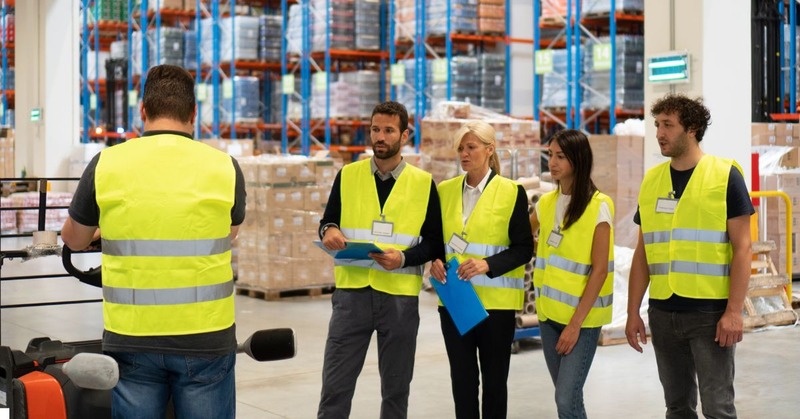
Setting up an effective pick, pack, and ship process can be complex, especially for larger operations. This complexity might require significant initial investment in technology and training.
Dependency on Technology
The efficiency of this process often relies heavily on technology, such as WMS and automated picking systems. This dependency can be a risk if there are technical failures or disruptions.
Space Requirements
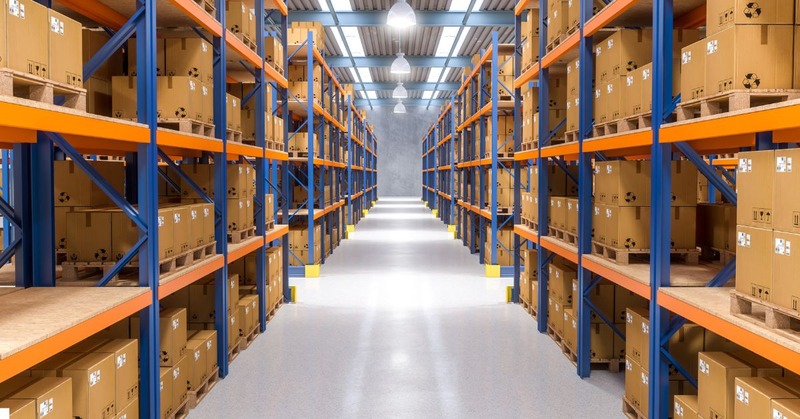
Effective pick, pack, and ship operations may require more space than traditional shipping methods, as they need distinct areas for each stage of the process. This might not be feasible for businesses with limited warehouse space.
Potential for Errors
While the process aims to minimize errors, the involvement of multiple stages and reliance on accurate inventory and order data can still lead to mistakes. Errors in picking or packing can result in incorrect shipments, affecting customer satisfaction.
Understanding these benefits and downsides will help businesses make informed decisions about whether the pick, pack, and ship process is suitable for their specific needs and operational capacities.
How to Know if the Pick, Pack, and Ship Process Meets My Warehousing Needs
When deciding whether the pick, pack, and ship process is suitable for your business needs, there are several key factors to consider that align with user pain points and intents:
Volume and Variety of Orders
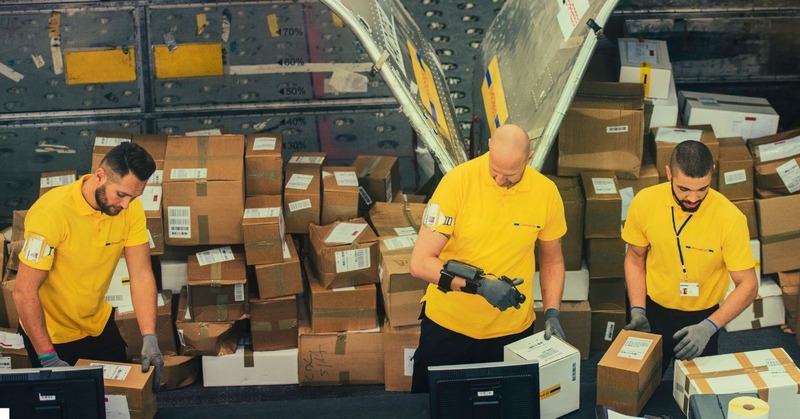
If your business handles a high volume of orders or a wide variety of products, a well-structured pick, pack, and ship process can help streamline operations and improve accuracy in fulfilling orders.
Complexity of Inventory Management
Businesses with complex inventory management might benefit from this process, especially those requiring detailed tracking and efficient handling of diverse products.
Customer Delivery Expectations
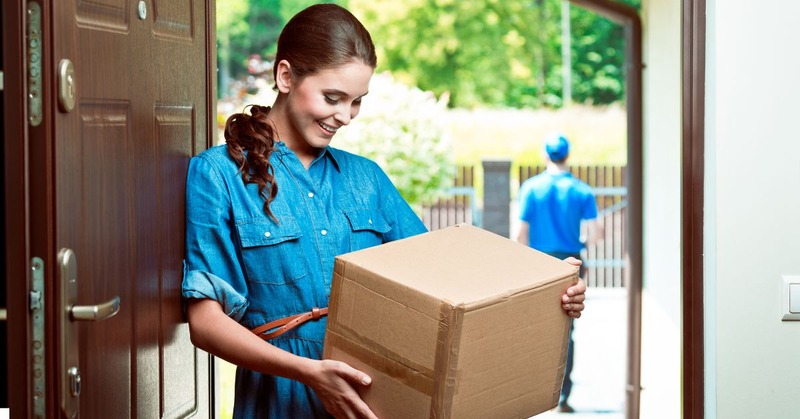
If timely delivery is crucial for customer satisfaction in your industry, this process might be essential. It helps in managing logistics efficiently, ensuring that products are picked, packed, and shipped promptly.
Scalability Needs
For businesses looking to scale up, the pick, pack, and ship process, integrated with advanced warehouse management systems, can accommodate growing order volumes and operational complexities.
Cost Considerations
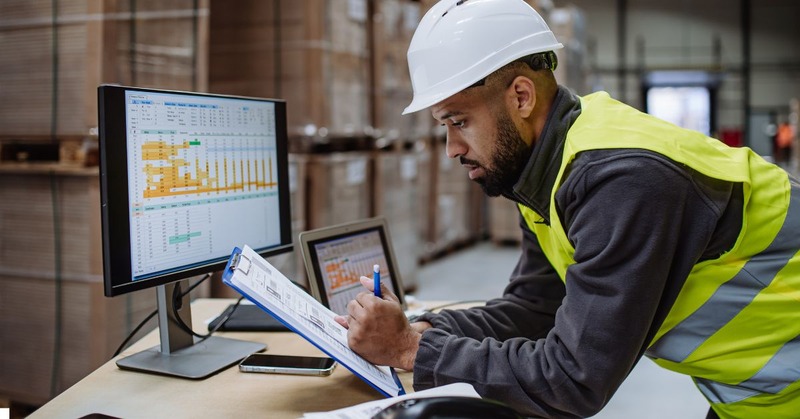
Itâs vital to consider whether the initial and ongoing costs of implementing and maintaining a pick, pack, and ship process will be outweighed by the efficiency and customer satisfaction gains. This includes the investment in technology, training, and possibly more sophisticated infrastructure.
Technological Integration
The extent to which your current systems can integrate with pick, pack, and ship technologies is also important. Efficient integration can significantly enhance order processing speeds and accuracy.
Error Reduction and Quality Control
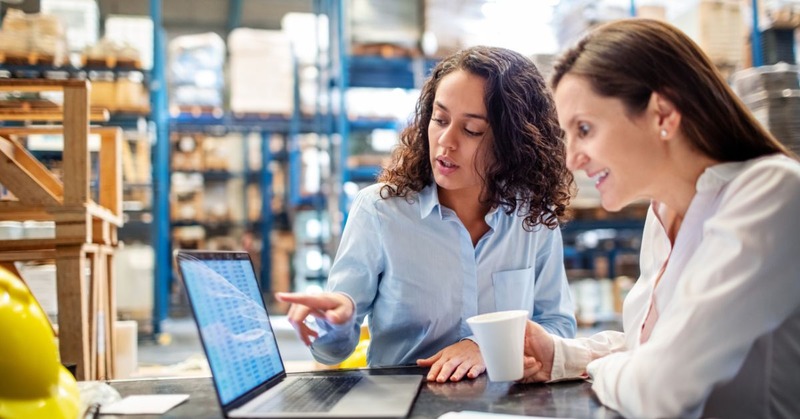
If your business suffers from high rates of shipping or packing errors, implementing a robust pick, pack, and ship process with strong quality controls can reduce these issues and improve overall customer satisfaction.
FAQs
What is the best way to train staff for efficient picking and packing?
Training staff for efficient picking and packing involves a combination of hands-on practice, clear guidelines, and regular updates on new technologies or processes. Incorporating simulation-based training and periodic refresher courses can also help maintain high standards of efficiency and accuracy.
How can small businesses optimize their pick, pack, and ship process without significant investment?
Small businesses can optimize their process by implementing simple organizational tools like color-coding, clear labeling, and dedicated packing stations. Additionally, focusing on inventory accuracy and using software that integrates with existing systems can improve efficiency without large capital investments.
How can technology further enhance the pick, pack, and ship process in the future?
Future enhancements could include greater automation with robots and drones for picking and packing, advanced AI for inventory management and demand forecasting, and increased use of blockchain for more secure and transparent tracking of shipments.
Conclusion
The "pick, pack, and ship" process is vital for efficient and accurate order fulfillment in e-commerce. Mastering this process enhances customer satisfaction but comes with challenges like technology integration, managing seasonal demand, and scaling operations.
Packiyo's cloud-based Warehouse Management System (WMS) offers a solution to these challenges. With real-time inventory management, seamless e-commerce integration, and an intuitive interface, Packiyo helps streamline operations, reduce errors, and improve efficiency.
If you're looking for related topics, check out our blog where we cover subjects such as 'batch picking' and 'zone picking.'
We hope we helped you understand this topic. If you have any questions, don't hesitate to reach out!