Have you ever faced frustrating delays waiting for a package, or managed inventory only to have a crucial shipment arrive late?
These are common experiences highlighting the issue of supply chain bottlenecks—points where delays disrupt the smooth flow of goods, leading to increased costs and customer dissatisfaction.
In our interconnected world, a minor disruption in one area can cascade into widespread delays and inefficiencies. Understanding the causes and impacts of these bottlenecks, as well as strategies to overcome them, is crucial for both businesses and consumers.
This article delves into the root causes, effects, and solutions to supply chain bottlenecks, offering practical insights to help you navigate and mitigate these challenges effectively.
What are Supply Chain Bottlenecks?
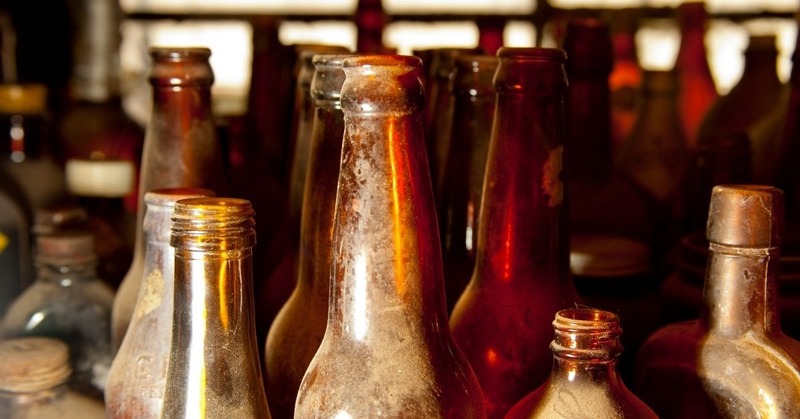
Supply chain bottlenecks occur when disruptions or inefficiencies at any point in the supply chain impede the smooth flow of goods, leading to delays, increased costs, and reduced operational efficiency.
These bottlenecks can be minor, like a broken conveyor belt in a warehouse that slows down operations but doesn't stop them, or major, such as a significant event blocking a key shipping route, halting the supply chain completely.
Apart from these, bottlenecks within the supply chain can severely disrupt business operations, leading to delays, increased costs, and customer dissatisfaction.
Causes
Common causes of bottlenecks include labor shortages, inadequate infrastructure, inefficient processes, and unexpected increases in demand.
Here's a more in-depth take below:
External Shocks
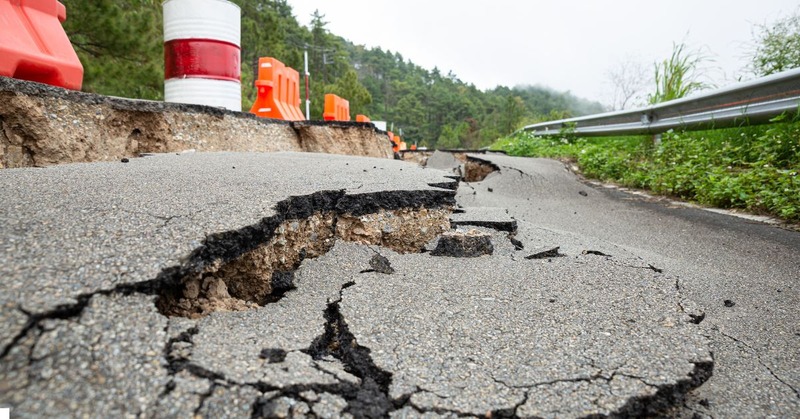
Events like earthquakes, floods, or political unrest can disrupt transportation and production, impacting the entire supply chain.
Demand Surges
Unexpected increases in product demand can overwhelm your supply chain, leading to shortages and delays in delivery.
Logistical Issues
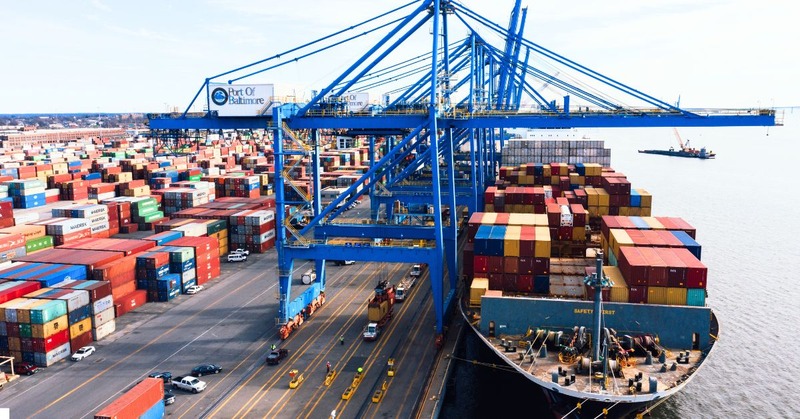
Problems such as insufficient transportation, port congestion, or shipping delays can slow down the entire supply chain process.
Supplier Reliance
Depending too much on one supplier or a few suppliers can create risks. If that supplier faces issues, your supply chain could suffer significantly.
ALSO READ: What’s the Difference Between Upstream and Downstream Supply Chain?
Operational Inefficiencies
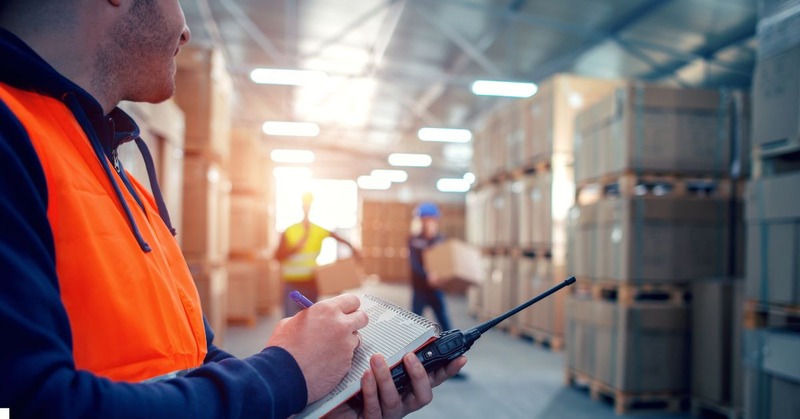
Poor warehouse maintenance, unclear communication among partners, and inadequate production capacity can all cause internal slowdowns.
Technological Limitations
Lack of advanced technology can lead to inefficient logistics management. Investing in technologies like pick to light systems and enhancing warehouse KPIs can improve accuracy and speed in the fulfillment processes.
Recent Examples of Bottlenecks in the Supply Chain
To understand even further how detrimental bottlenecks within the supply chain can be, here are some recent examples that you might definitely know and have experienced:
COVID-19 Pandemic (2020 onwards)
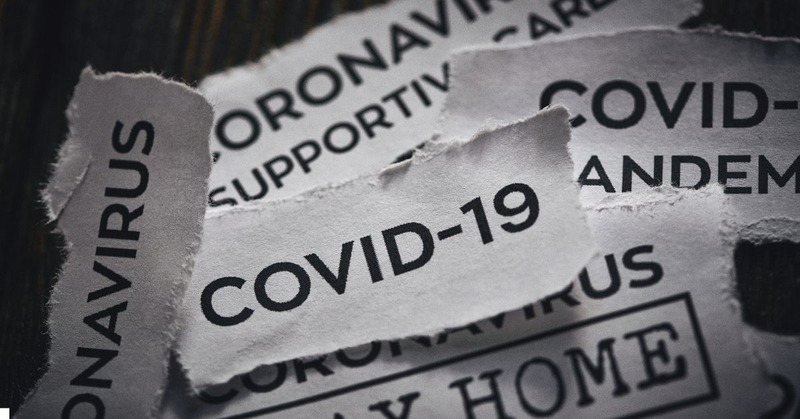
The pandemic significantly disrupted global supply chains due to lockdowns, labor shortages, and surges in online shopping. These factors led to closed factories, reduced production capabilities, and immense pressure on the transportation of goods and raw materials.
Suez Canal Blockage (March 2021)
The Ever Given, a massive container ship, got stuck in the Suez Canal, halting the flow of goods through one of the world's busiest waterways. This incident caused significant delays and highlighted the vulnerability of global trade routes to unexpected events.
Global Labor Shortages (2021 onwards)
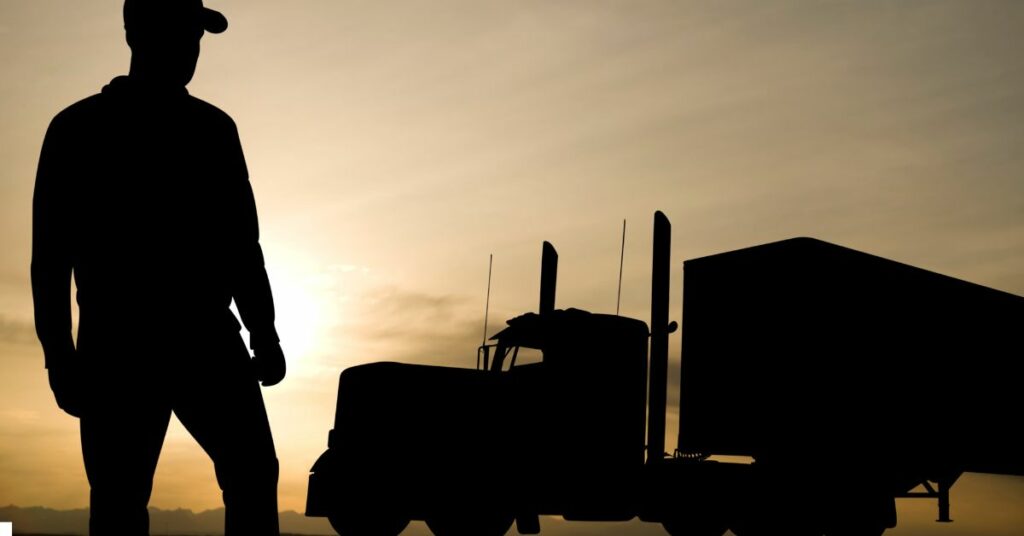
Triggered by the pandemic, labor shortages affected various sectors, including transportation and manufacturing. This has been particularly evident in regions like Europe, which experienced a significant shortage of truck drivers, further straining supply chains.
Geopolitical Tensions and Trade Barriers (2022)
Events like Russia’s invasion of Ukraine disrupted the supply of commodities and raw materials, forcing businesses to seek alternative suppliers and adjust their strategies. Additionally, ongoing trade tensions between major economies have intermittently affected global supply chains.
How to Overcome Bottlenecks in Supply Chain
Now that you understand what supply chain bottlenecks are, their common causes, and examples, let's now go through how you can actually overcome them:
1. Analyze and Predict Bottlenecks
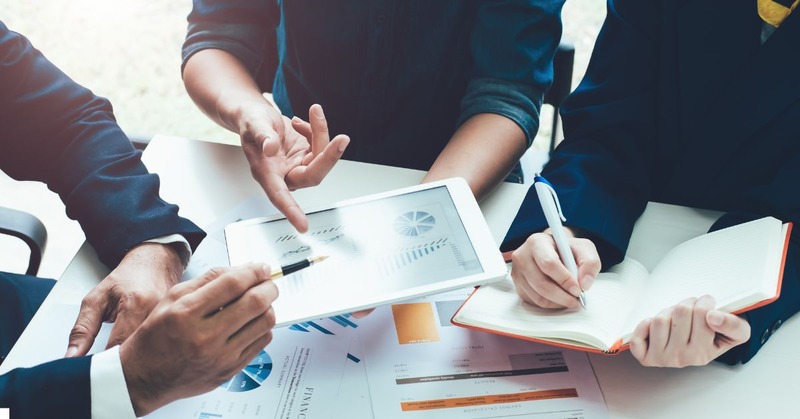
Conduct thorough analyses to pinpoint bottlenecks and use predictive analytics to foresee potential issues. This helps in preemptively addressing problems before they impact the supply chain.
2. Utilize Advanced Data Insights
Use state-of-the-art data analytics to monitor and manage your supply chain. Centralizing data on a cloud platform enhances accessibility and speeds up decision-making processes.
3. Partner with Skilled 3PL Providers
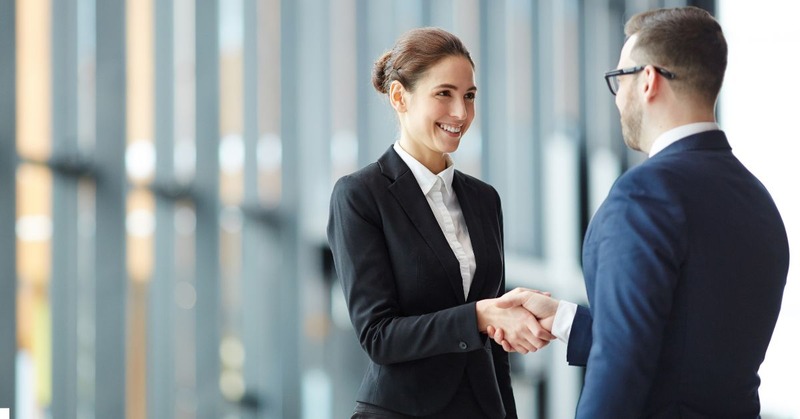
Collaborate with third-party logistics (3PL) providers that have a robust technological framework and extensive experience. Choose partners who can adapt to changing demands and efficiently handle various fulfillment operations.
4. Create Flexible Supply Chain Plans
Develop adaptable plans that include effective responses to potential disruptions. Use the expertise of 3PLs to craft strategies that bolster your supply chain against unforeseen challenges.
5. Ensure Transparency and Adaptability
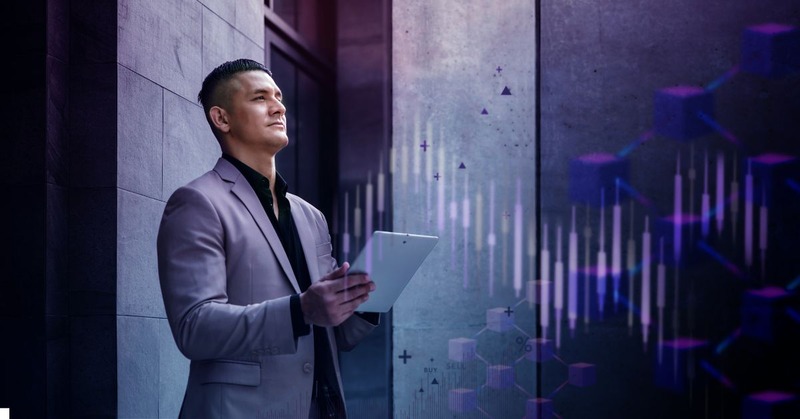
Invest in technologies that enhance real-time visibility and flexibility of your operations. This allows for quick adjustments and fosters a proactive approach to managing disruptions.
6. Optimize Inventory and Production
Apply predictive analytics to manage inventory effectively, avoiding overstocking or shortages. Automate production processes where possible to increase efficiency and output.
7. Streamline Transportation and Logistics
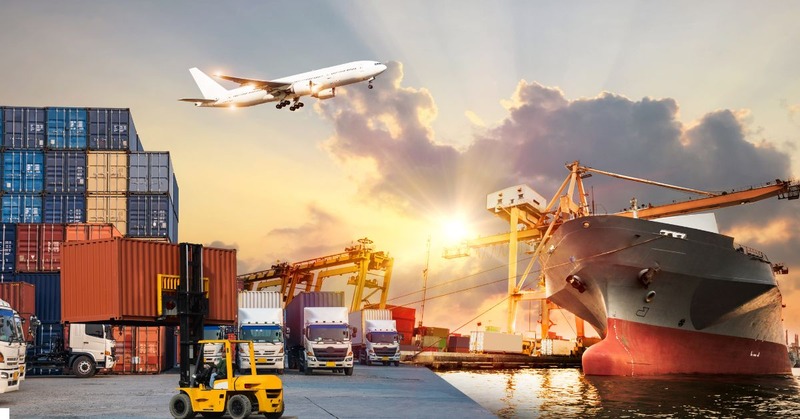
Improve your logistics setup by optimizing routes, partnering with reliable carriers, and incorporating efficient last-mile delivery solutions to meet customer expectations.
8. Develop Robust Contingency Plans
Prepare for disruptions with detailed contingency plans that cover alternative suppliers and emergency strategies. Regularly update these plans to adapt to new risks and ensure they provide effective safeguards.
FAQs
What are some common mistakes companies make in supply chain management that lead to bottlenecks?
Common mistakes include failing to forecast demand accurately, inadequate communication across the supply chain, and not having sufficient contingency plans in place. These oversights can lead to inventory mismanagement and delays in production or delivery.
Can supply chain bottlenecks affect a company's competitive edge? How?
Yes, bottlenecks can significantly impact a company’s ability to meet customer demands timely and efficiently, leading to customer dissatisfaction and lost sales opportunities. Competitors who manage their supply chains more effectively may provide faster, more reliable service, thereby gaining a competitive advantage.
What technologies are crucial for identifying supply chain bottlenecks?
Technologies like real-time data analytics, artificial intelligence (AI), and Internet of Things (IoT) devices play crucial roles. They help monitor supply chain operations, predict potential disruptions, and provide actionable insights to mitigate risks before they cause significant issues.
How can small to medium enterprises (SMEs) manage supply chain bottlenecks effectively?
SMEs can manage bottlenecks by leveraging cloud-based supply chain solutions that offer scalability and flexibility, maintaining strong relationships with multiple suppliers to reduce dependency, and utilizing 3PL providers to enhance logistics and distribution efficiency.
How does customer demand forecasting help prevent supply chain bottlenecks?
Effective demand forecasting allows companies to align their inventory and production schedules with anticipated market demands, thus preventing overstocking or stockouts. Advanced forecasting tools analyze historical sales data, market trends, and other relevant factors to predict future demand accurately.
Conclusion
Supply chain bottlenecks can disrupt business operations and impact customer satisfaction. To manage these challenges effectively, incorporating a robust Warehouse Management System (WMS) like Packiyo can be crucial.
We at Packiyo offers comprehensive solutions to streamline inventory management, optimize shipping processes, and ensure seamless data integration with other platforms. Its automation features reduce manual errors and speed up order processing, while real-time inventory tracking prevents stockouts and overstock issues.
For third-party logistics providers, Packiyo's flexible billing and client management tools promote transparency and efficiency.
Check out our blog if you want to read more topics that are similar to this. In there, we cover topics like 'What's the Difference Between Supplies and Inventory?' and 'What is Warehouse Ergonomics?', and maybe more.
We hope that we've helped you understand how daunting supply chain bottlenecks can be and how you can overcome them. Check through our site, and we're looking forward to having you read our next article. Take care!