Imagine you’re managing a busy warehouse, and despite your best efforts, errors in order picking are leading to delays, customer complaints, and increased costs.
Your team spends valuable time looking at lists or screens, manually entering data, and correcting mistakes. This scenario is all too common in many warehouses today.
Seeking a solution that streamlines operations, improves accuracy, and boosts productivity, you come across the concept of voice picking.
This picking strategy promises to streamline operations, improve accuracy, and boost productivity.
But how does this work, exactly?
In this article, we’ll explain how voice picking works, its benefits, and whether it’s the right fit for your warehouse.
Table of Contents
- What is Voice Picking?
- How Does Voice Picking Work?
- What are the Benefits of Using Voice Picking?
- How to Know If You Need Voice Picking in Your Warehouse
- Conclusion
- FAQs
What is Voice Picking?
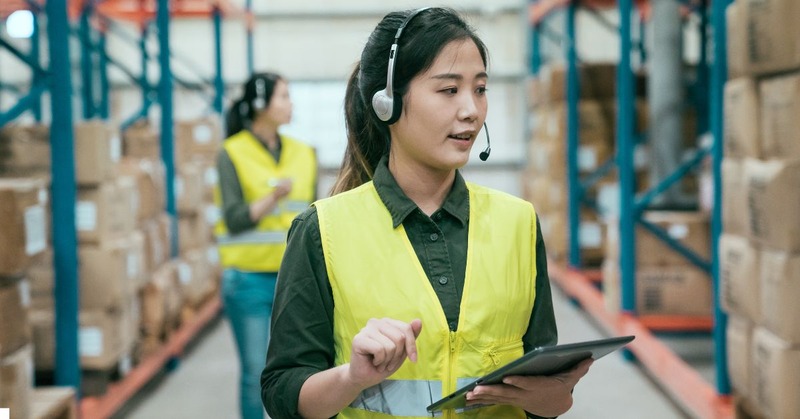
Voice picking is a technology used in warehouse operations that enables workers to receive and confirm picking tasks through voice commands, using a headset connected to a mobile device.
This system integrates with warehouse management systems (WMS) or enterprise resource planning (ERP) software to provide real-time, hands-free instruction to pickers.
Basically, voice picking is like having a GPS for warehouse work.
Just as a GPS guides you through traffic, telling you where to turn to reach your destination efficiently, a voice picking system directs warehouse workers to the right spots and tells them what items to pick.
This keeps their hands free and eyes focused on their surroundings, similar to how you can keep your eyes on the road while listening to navigation instructions.
How Does Voice Picking Work?
To further expound on how this picking process works, let's go through the step-by-step ways on how voice picking is achieved:
1. Integration with WMS/ERP
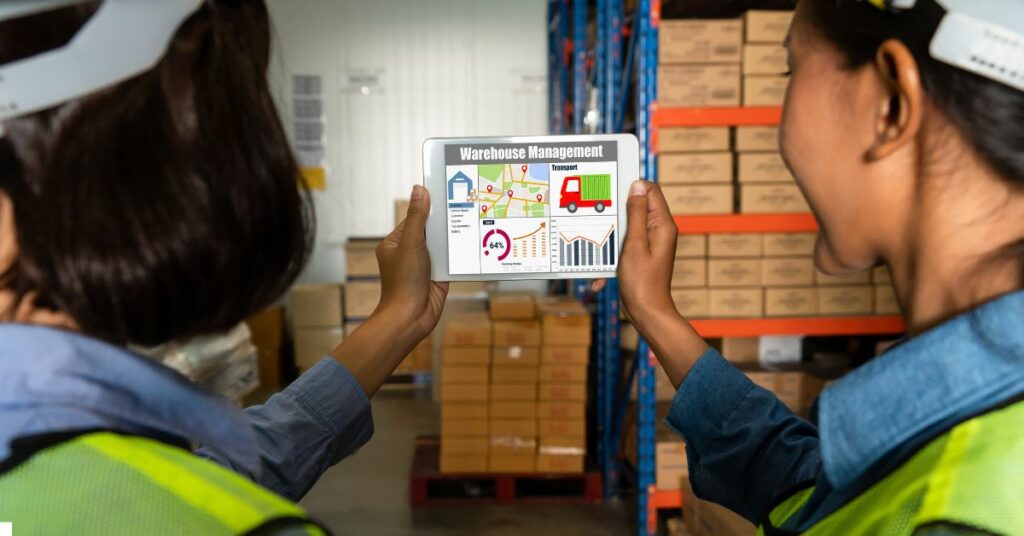
The journey begins with the voice picking system integrating seamlessly with the warehouse's existing Warehouse Management System (WMS) or Enterprise Resource Planning (ERP) software.
This integration allows the system to pull order details, inventory data, and workflow information to organize tasks efficiently.
2. Equipping Workers
Warehouse workers are equipped with headsets connected to industrial microphones. These devices are linked to mobile terminals that carry the voice application. These terminals may be handheld or worn on the body, allowing for complete hands-free operation.
3. Receiving Instructions
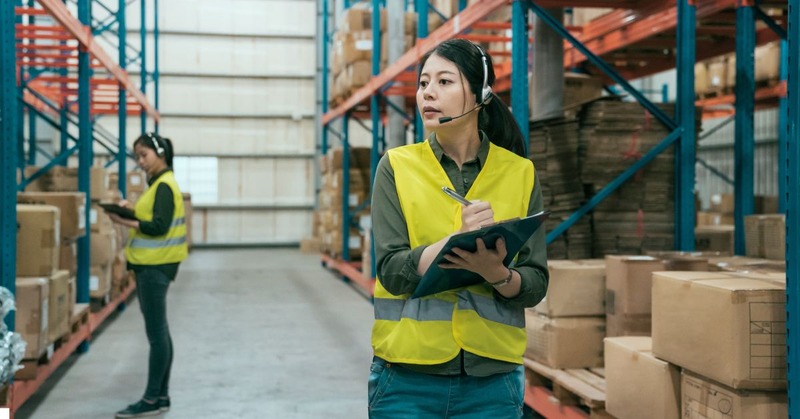
Once the setup is complete, the voice system begins distributing tasks.
Workers receive clear, spoken instructions through their headsets—directing them to specific locations and detailing the items they need to pick. This guidance can be in simple, conversational language that is easy to understand.
4. Interactive Workflow
As workers follow these voice commands, they interact with the system by confirming actions or asking for repetitions if needed. This is usually done by speaking into the microphone. The system uses advanced speech recognition to understand and respond to the worker’s voice.
5. Task Confirmation
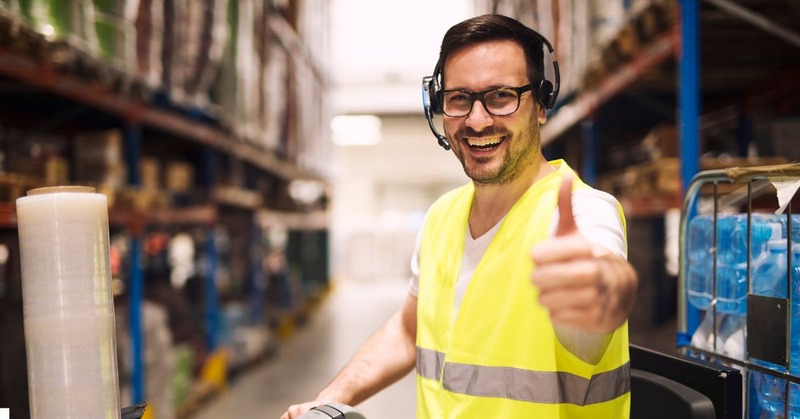
For accuracy, workers confirm the location and item details by voicing check strings or item codes. The system verifies these details against its records to ensure that the correct items are being picked.
6. Quantity Confirmation
Workers are also prompted to confirm the quantity of each item picked. This step is crucial for maintaining inventory accuracy and order fulfillment precision.
7. Optimized Routing
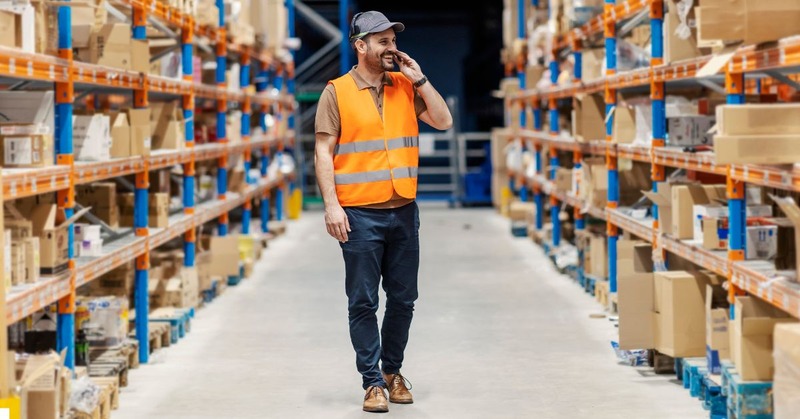
The voice system continuously guides workers to their next locations, optimizing travel paths within the warehouse. This routing is designed to minimize walking distance and maximize picking efficiency.
8. Continuous Feedback and Updates
Every interaction and confirmation is recorded by the system. This data feeds back into the WMS/ERP, providing real-time updates on task progress and inventory levels.
9. Management Oversight
The system includes tools for management to monitor operations, track worker productivity, and analyze workflow efficiency. These tools help in making informed decisions to further optimize warehouse operations.
Once all assigned tasks are completed, the system can guide workers to areas for finalizing the order, such as packing or staging areas. The system ensures that all picked items are accounted for and properly processed before shipment.
What are the Benefits of Using Voice Picking?
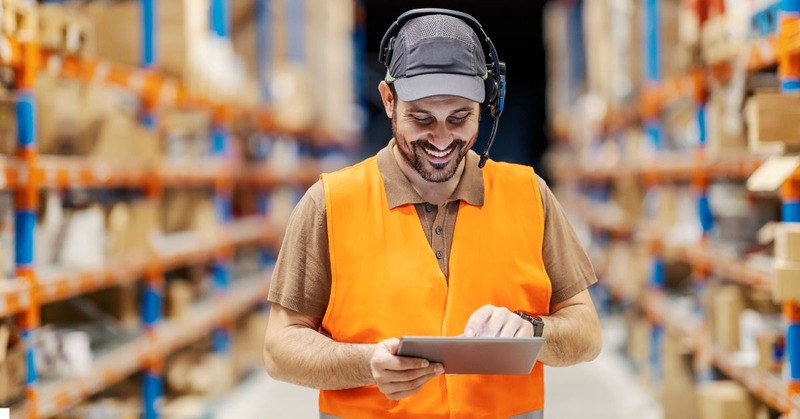
Alright. You now understand what voice picking is and how it exactly works, but what are the advantages to this picking method?
Well, here's a deeper look into why warehouse managers such as yourself or other stakeholders should consider implementing voice-directed picking systems:
Enhanced Productivity and Efficiency
Voice picking systems allow warehouse workers to operate hands-free and with their attention fully on the task, eliminating the need to handle paper lists or scanners.
This setup significantly boosts productivity by minimizing distractions and reducing the time spent on manual data entry or scanning barcodes.
Increased Accuracy
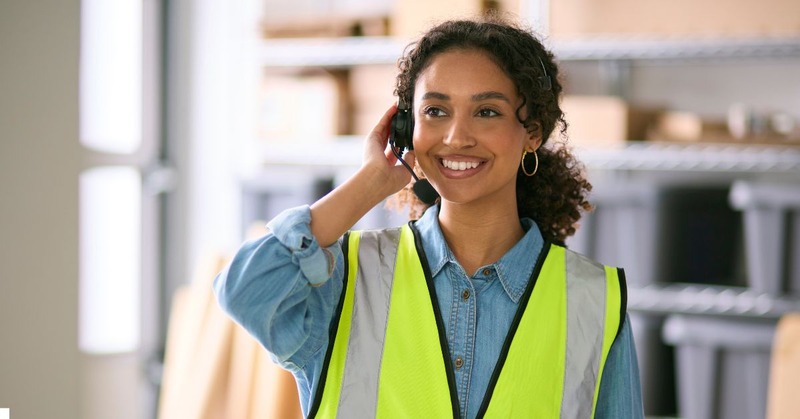
The precision of picking tasks is crucial for reducing waste and improving customer satisfaction. Voice picking systems enhance accuracy by requiring verbal confirmations for each picking action, which reduces errors typically caused by manual processes.
Some distribution centers have observed error reductions of up to 80% with voice picking, achieving near-perfect accuracy rates.
Safety Improvements
With voice picking, operators' hands and eyes are free, allowing them to be more aware of their surroundings and thus reducing the likelihood of accidents. This is particularly important in environments where workers are handling large or hazardous items.
Reduced Training Time
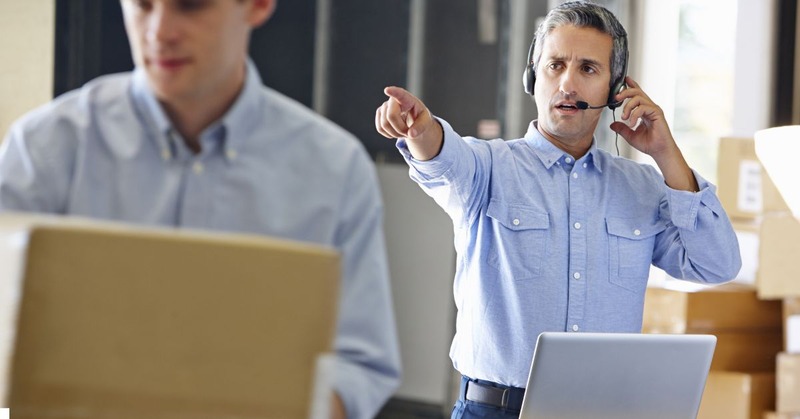
Training new staff becomes simpler and quicker with voice picking systems. The intuitive nature of voice commands means that workers can become proficient in their tasks faster, which is especially beneficial during peak periods or in high turnover environments.
Flexibility and Scalability
Voice picking technology is adaptable to various operational needs and can be integrated with existing warehouse management systems without requiring major changes. This flexibility ensures that businesses can respond effectively to seasonal fluctuations and changing market demands.
Better Inventory Management
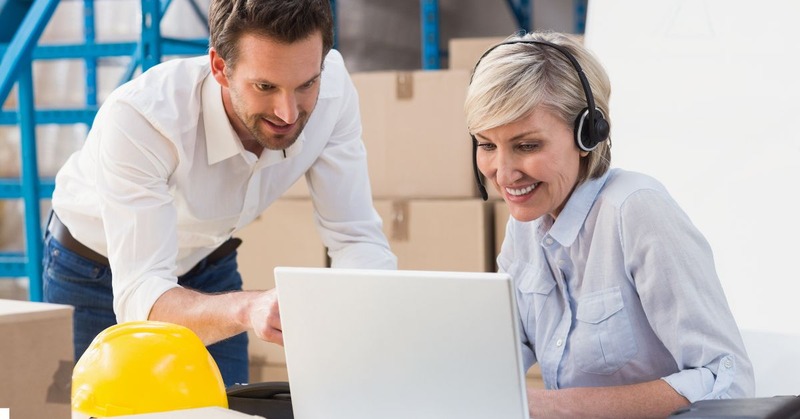
Integrating voice picking systems with warehouse management software allows for real-time updates to inventory levels. This immediate feedback improves inventory accuracy and helps prevent issues such as stockouts or overstock, optimizing the supply chain.
How to Know If You Need Voice Picking in Your Warehouse
Considering voice picking technology for your warehouse operations after reading through everything? Here are the top signs that you should identify first to know whether or not you actually need a voice picking system.
High Error Rates in Current Picking Processes
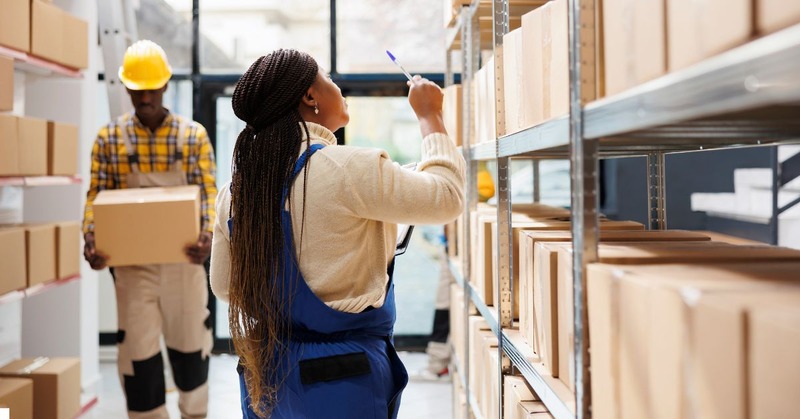
If your warehouse experiences high error rates with traditional picking methods such as manual data entry or barcode scanning, voice picking could significantly reduce those errors.
Voice picking minimizes the risk of manual entry mistakes by using verbal confirmations for each pick, enhancing accuracy and reducing costly corrections.
Need for Improved Worker Productivity
If your operation struggles with productivity, voice picking can offer a solution. This technology enables workers to perform tasks hands-free and without the need to look away from their work to consult paperwork or devices.
This can lead to quicker task completion and a smoother workflow, ultimately boosting productivity levels.
Complex or Expanding Operations
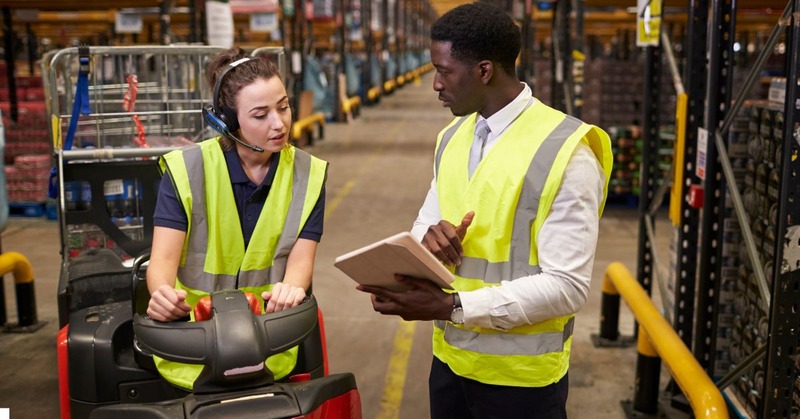
For warehouses experiencing growth or managing a vast array of products, voice picking can simplify the complexities associated with scaling. It's particularly effective in environments where rapid onboarding of new staff is necessary or where operations are too vast for traditional picking methods to manage efficiently.
High Training and Labor Costs
If training new staff is time-consuming and costly, voice picking can reduce these expenses. The technology is intuitive and can significantly shorten the learning curve for new employees, allowing them to become productive more quickly than with traditional systems.
Seasonal Volume Fluctuations
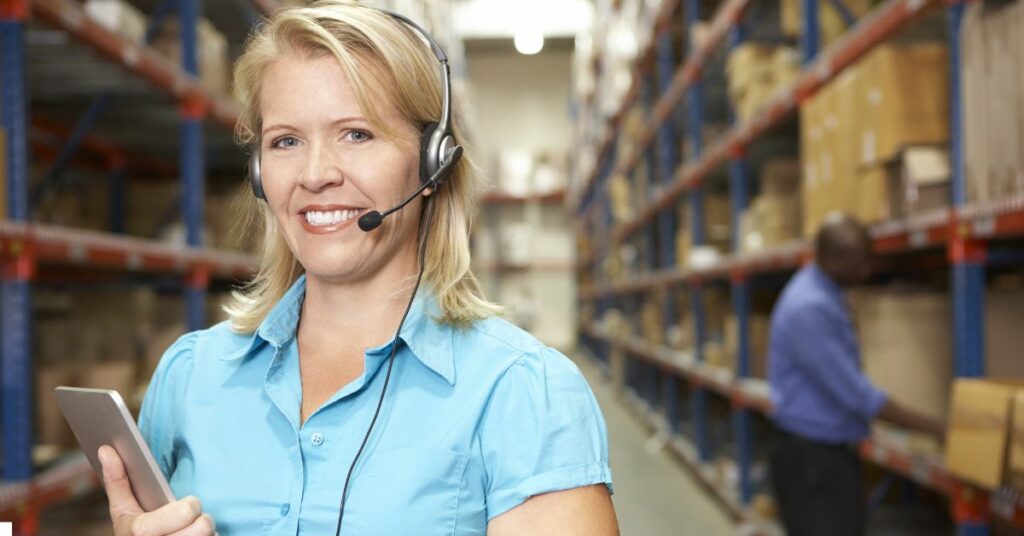
If your warehouse operations see significant peaks and troughs — such as during holiday seasons or special promotions — voice picking can help manage these fluctuations more efficiently.
The system's flexibility allows temporary staff to quickly adapt and perform at high efficiency, helping to handle high volume periods without a permanent increase in labor costs.
Conclusion
Voice picking technology is a game-changer for warehouse operations, enhancing productivity, accuracy, and safety. It streamlines the picking process by enabling workers to focus on tasks without the distractions of manual data entry.
To maximize these benefits, consider integrating our comprehensive Warehouse Management System (WMS) here at Packiyo.
Our mobile smart picking capabilities work seamlessly with voice picking systems, providing flexibility and efficiency. The Co-Pilot automation feature handles repetitive tasks, ensuring smooth operations. Real-time inventory tracking from Packiyo keeps data accurate, reducing errors and enhancing efficiency.
The Rapid Pack & Ship feature ensures that items picked with voice commands are swiftly packed and shipped, maintaining high accuracy and speed. Additionally, Packiyo integrates with popular eCommerce platforms, ensuring a unified approach to order and inventory management.
Contact us to learn more about how these solutions can meet your warehouse management needs and help achieve your operational goals.
Check out our blog if you want to read related topics similar to this one, such as 'what is a bottleneck in the supply chain', 'inventory vs supplies', and more.
FAQs
How does voice picking integrate with other automated systems in a warehouse?
Voice picking systems can be seamlessly integrated with various automated systems such as robotic process automation (RPA), automated storage and retrieval systems (ASRS), and conveyor systems.
This integration enhances overall workflow efficiency by synchronizing voice commands with automated movements, reducing manual intervention, and streamlining the path from picking to shipping.
What are the challenges of implementing voice picking in a multilingual workforce?
Implementing voice picking in a diverse linguistic environment involves ensuring the voice recognition software accurately understands and processes multiple languages and dialects.
This may require additional calibration and customization of the software to handle varied accents and speech patterns, ensuring that all workers can interact effectively with the system without miscommunications that could lead to errors or inefficiencies.
Can voice picking technology be adapted for outdoor use or in large-scale storage areas?
Yes, voice picking technology can be adapted for use in outdoor storage areas or large-scale facilities by employing robust, weather-resistant hardware and enhancing signal transmission capabilities to cover larger distances.
Special adaptations might include long-range wireless networks and enhanced audio equipment to cope with ambient noise and environmental conditions.
What impact does voice picking have on employee satisfaction and turnover?
Voice picking generally increases employee satisfaction by reducing the physical and mental strain associated with traditional picking methods. The hands-free, eyes-free nature of the technology allows workers to perform their tasks more comfortably and efficiently, potentially leading to lower turnover rates.
Continuous interaction with technology that facilitates work can improve job satisfaction, as workers feel more supported and valued.
How do companies measure the ROI of implementing voice picking technology?
Companies measure the ROI of implementing voice picking technology by analyzing several key performance indicators (KPIs), including but not limited to, increases in picking accuracy and productivity, reductions in training time and operational errors, and improvements in inventory management.
Additionally, factors like employee retention rates and customer satisfaction levels due to faster and more accurate order fulfillment can also play a role in determining the financial benefits.
This process illustrates how voice picking not only simplifies the picking process but also integrates deeply with other warehouse operations, supporting a comprehensive, efficient, and error-reduced workflow. This technology not only speeds up the picking process but also enhances overall operational efficiency, leading to significant gains in productivity and accuracy in warehouse management.