As warehouse operations face the relentless push for better efficiency and productivity, it's no surprise that you, someone who's working within the industry, would find ways to better optimize your tasks.
Implementing KPIs within your warehouse will not only solve this issue but will also improve pre-existing KPIs that are already present.
But what are 'warehouse KPIs', exactly?
To fully understand this topic, you'd have to read through each and every one below.
What are Warehouse KPIs?
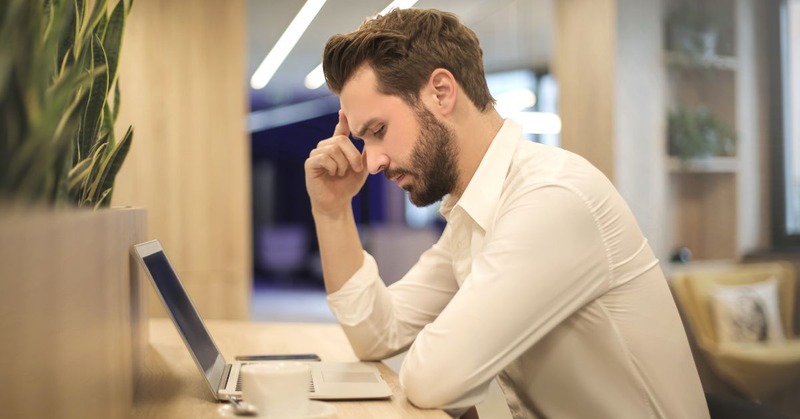
Warehouse Key Performance Indicators (KPIs) are specific, quantifiable metrics used to measure, monitor, and assess the efficiency and effectiveness of a warehouse's operations.
These indicators cover various aspects of warehouse management, including inventory control, order fulfillment, receiving and put-away efficiency, safety standards, and overall operational performance.
Why Use It?
Implementing KPIs in warehouse operations allows managers and stakeholders to make data-driven decisions, identify areas for improvement, and track the impact of implemented changes over time.
By focusing on key metrics, warehouses can optimize their operations, reduce costs, and improve customer satisfaction.
Here are additional reasons why warehouse managers should implement these KPIs:
Improved Operational Efficiency
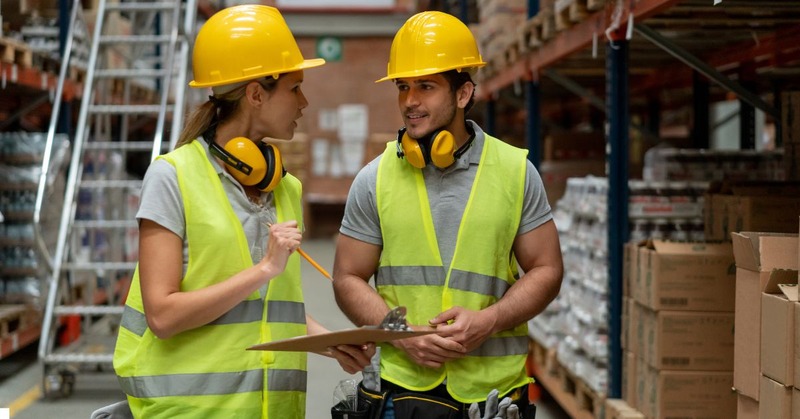
KPIs help identify bottlenecks and inefficiencies in warehouse operations, allowing for targeted interventions that streamline processes and improve throughput.
Enhanced Inventory Management
Tracking KPIs related to inventory, such as turnover rates and accuracy, enables better inventory control, reduced carrying costs, and minimized stockouts or overstock situations.
Increased Customer Satisfaction
By monitoring KPIs associated with order fulfillment and delivery, warehouses can ensure timely and accurate orders, leading to higher customer satisfaction and loyalty.
Cost Reduction
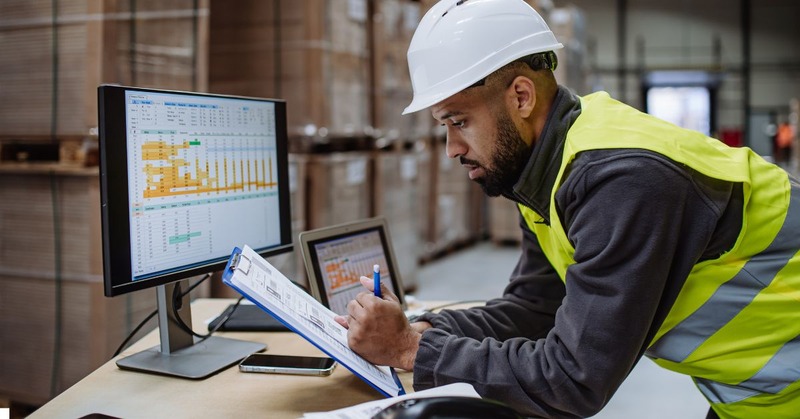
Efficiency improvements and optimization of inventory management lead to significant cost savings. KPIs help pinpoint areas where costs can be reduced without compromising service quality.
Safety and Compliance
Safety-related KPIs encourage a safer working environment, reducing the risk of accidents and ensuring compliance with regulations and standards.
What Are the Most Important Warehouse KPIs That You Should Use?
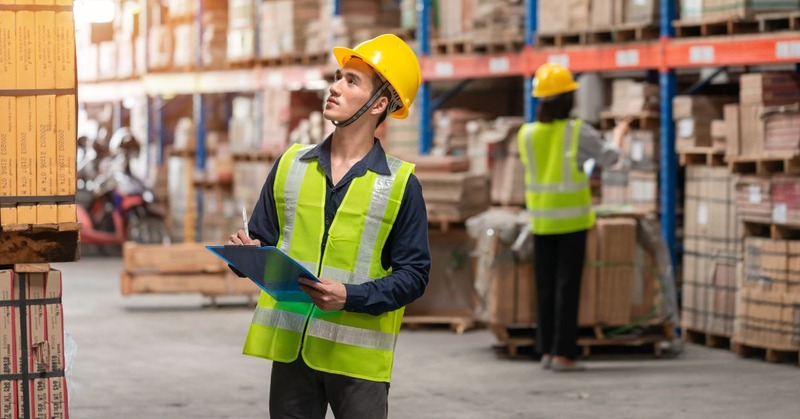
By focusing on the most impactful metrics, warehouse managers can streamline workflows, enhance productivity, and ultimately achieve better financial outcomes and customer satisfaction.
Here is the list of KPIs that you should be monitoring and identifying in your warehouse:
Inventory KPIs
Inventory KPIs are crucial metrics that help businesses monitor and manage their inventory levels, costs, and processes effectively.
They provide insights into how efficiently inventory is being managed and how it contributes to the overall business performance.
Here's a brief overview of the key Inventory KPIs:
1. Carrying Cost of Inventory
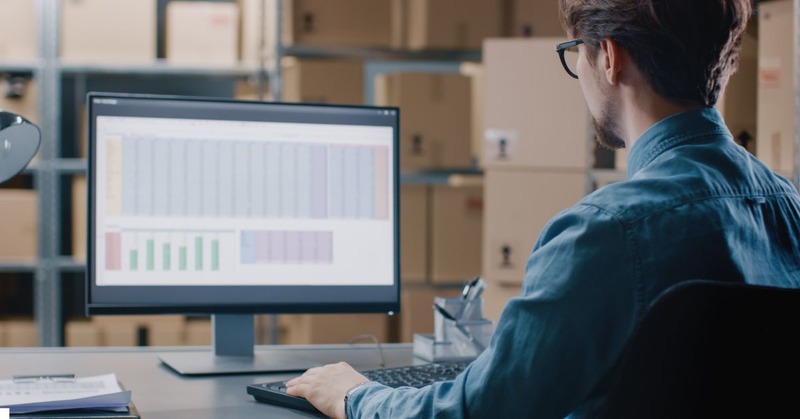
This metric quantifies the total cost of holding inventory, including storage, handling, insurance, and depreciation. It helps businesses understand the financial impact of the inventory they keep on hand.
How to Calculate: Add the inventory holding cost to the cost of goods sold, then divide by the total value of inventory.
2. Inventory Turnover
Inventory Turnover measures how often inventory is sold and replaced over a specific period. A higher turnover rate indicates efficient inventory management and sales processes, suggesting that stock is not sitting idle.
How to Calculate: Divide the cost of goods sold by the average value of your inventory.
3. Inventory-to-Sales Ratio
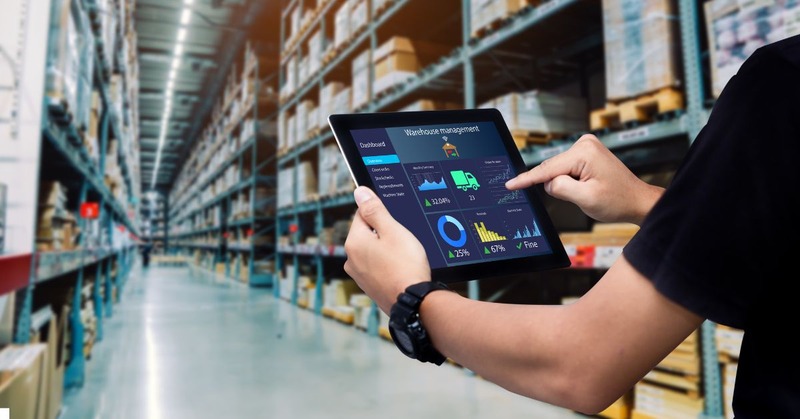
This ratio compares the amount of inventory a business has on hand to the amount it sells. It's a critical indicator of the balance between supply and demand, showing whether inventory levels are aligned with sales patterns.
4. Inventory Accuracy
Inventory Accuracy assesses the match between physical inventory counts and the inventory records in a company's database. High accuracy indicates effective inventory management, reducing the risk of stockouts or excess inventory.
How to Calculate: Divide the book-recorded inventory by the physically counted inventory, and then multiply by 100%.
Receiving KPIs
Receiving KPIs focus on measuring the efficiency and effectiveness of the processes involved in receiving goods and materials at a warehouse or distribution center.
These KPIs are vital for ensuring that incoming inventory is processed accurately and promptly, setting the stage for all subsequent warehouse activities.
Here's an overview of the key Receiving KPIs:
5. Receiving Efficiency
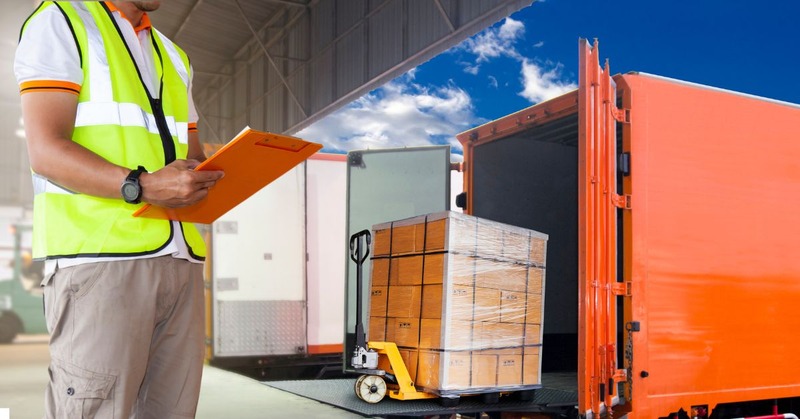
This metric evaluates how effectively a warehouse manages the receipt of goods, including unloading, inspection, and documentation. High receiving efficiency minimizes delays and errors, ensuring that inventory is available for sale or use as quickly as possible.
How to Calculate: Divide the quantity of inventory items received and inspected by the total duration taken for the process.
6. Receiving Cycle Time
Receiving Cycle Time measures the total time taken from the arrival of goods at the warehouse to the moment they are ready to be stocked on shelves. This KPI helps businesses identify bottlenecks in the receiving process and improve overall inventory management.
Put-away KPIs
Put-away KPIs track the efficiency and accuracy of storing incoming items in their designated locations within a warehouse or distribution center.
These metrics are critical for optimizing storage processes, ensuring inventory accuracy, and maintaining a well-organized warehouse.
Here's a quick look at the essential Put-away KPIs:
7. Accuracy Rate
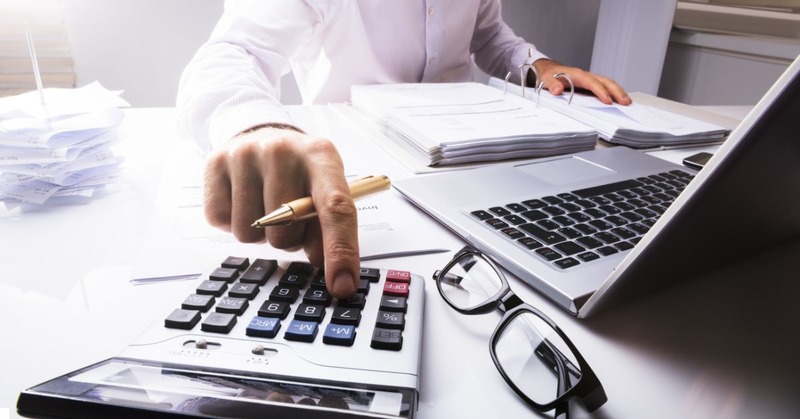
The Accuracy Rate measures the percentage of items correctly stored in their designated locations on the first attempt. High accuracy rates indicate efficient put-away processes and contribute to better inventory management and retrieval efficiency.
How to Calculate: Take the number of orders fulfilled without errors, divide by the total orders shipped, and multiply by 100%.
8. Put Away Cost per Line
This metric calculates the average cost associated with storing each line item in the warehouse. It includes labor, equipment, and overhead costs, providing insight into the efficiency of the put-away process and areas where cost reductions can be achieved.
9. Put Away Cycle Time
Put Away Cycle Time tracks the duration from when an item is received until it is successfully stored in its specific location. Shorter cycle times reflect more efficient put-away processes, reducing labor costs and increasing the readiness of inventory for sale or production.
How to Calculate: Divide the total duration from receiving inventory to its storage by the number of items involved.
Order Management KPIs
Order Management KPIs are crucial for monitoring and improving the processes involved in fulfilling customer orders.
These metrics help ensure that orders are processed efficiently, accurately, and cost-effectively, directly impacting customer satisfaction and operational efficiency.
Here's a brief overview of each KPI in this section:
10. Order Picking Accuracy
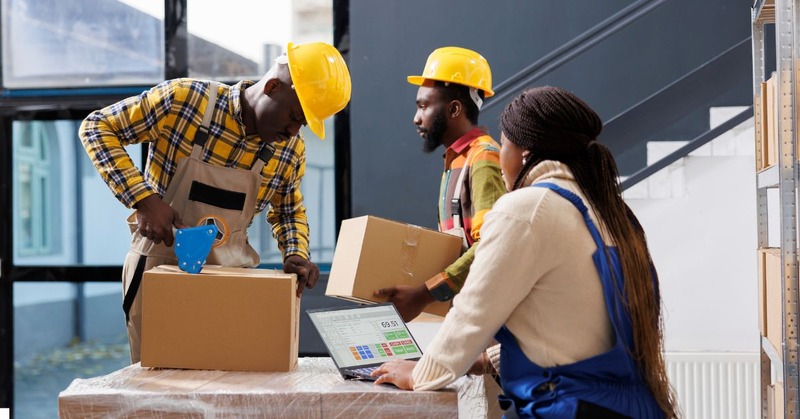
This metric measures the accuracy of the picking process, ensuring that the correct items and quantities are selected for customer orders. High order picking accuracy reduces errors, returns, and customer dissatisfaction.
How to Calculate: Divide the total number of orders picked correctly by the total number of orders picked, then multiply by 100%.
11. Total Order Cycle Time
Total Order Cycle Time tracks the duration from when an order is placed until it is fully processed and ready for shipment. This KPI is essential for identifying bottlenecks in the order fulfillment process and improving overall customer service.
How to Calculate: Add up the total time spent processing all orders and divide by the total number of orders.
12. Back Order Rate
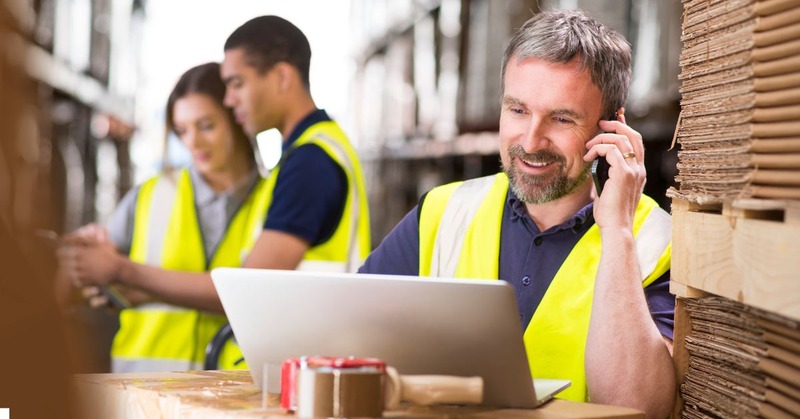
The Back Order Rate indicates the percentage of orders that cannot be fulfilled immediately due to inventory shortages. A lower back order rate suggests better inventory management and a higher level of customer service.
How to Calculate: Divide the number of backorders by the total number of orders, then multiply by 100%.
13. Fulfillment Accuracy Rate
Fulfillment Accuracy Rate assesses the percentage of orders correctly fulfilled in relation to total orders. It encompasses picking accuracy, packaging, and shipping, highlighting the efficiency of the order fulfillment process.
14. On-time Shipping Rate
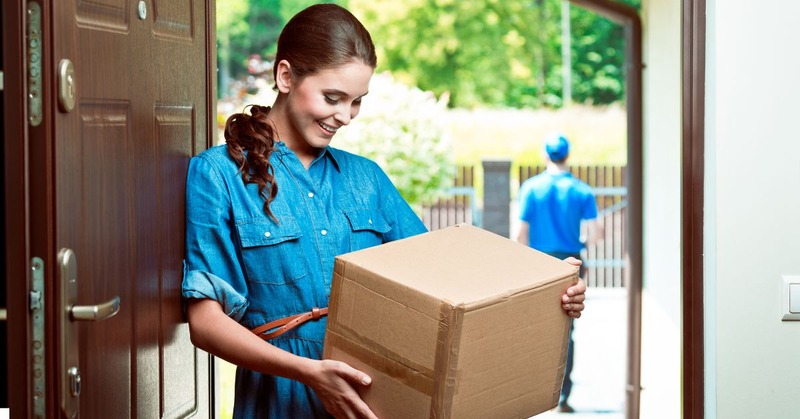
This KPI measures the proportion of orders shipped within the promised time frame, reflecting the efficiency of the shipping process and the company's reliability in meeting delivery commitments.
15. Cost per Order
Cost per Order calculates the total cost associated with processing an order, including picking, packing, shipping, and handling. This metric helps identify opportunities for cost savings and efficiency improvements in order fulfillment.
How to Calculate: Divide the total costs incurred in processing orders by the number of orders processed.
16. Rate of Returns
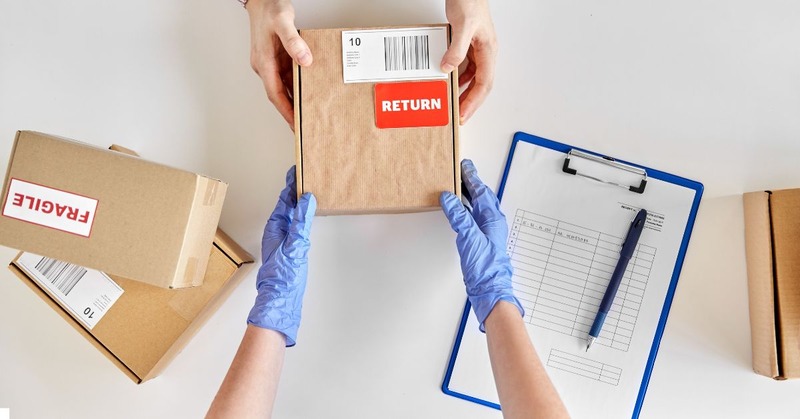
The Rate of Returns measures the percentage of sold items that are returned by customers. It serves as an indicator of product quality, order accuracy, and customer satisfaction, highlighting areas for improvement in product offerings and order management processes.
How to Calculate: Divide the number of orders that were returned by the total number of orders shipped, then multiply by 100%.
Safety KPIs
Safety KPIs are essential metrics that track and evaluate the effectiveness of a warehouse or distribution center's health and safety programs.
These KPIs aim to minimize workplace accidents and ensure a safe working environment for all employees.
Here’s an overview of the critical Safety KPIs:
17. Accidents per Year
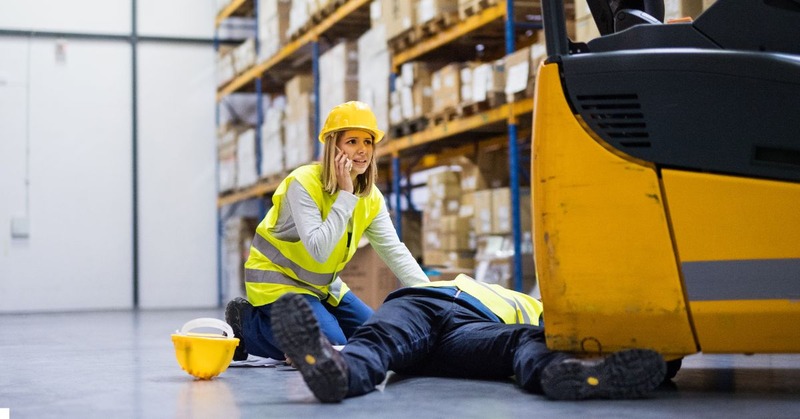
This metric counts the total number of reported accidents or incidents within a warehouse over a year. It is a crucial indicator of the overall safety of the work environment, with a lower number of accidents reflecting more effective safety measures and training.
18. Time Since Last Accident
Time Since Last Accident measures the number of days that have passed since the last recorded workplace accident or incident. This KPI serves as a motivational benchmark for employees and management to continuously improve safety practices, aiming to extend the accident-free period as much as possible.
Performance KPIs
Performance KPIs measure the overall efficiency and effectiveness of warehouse operations.
These metrics are crucial for optimizing workflows, maximizing resource utilization, and improving the bottom line.
Here’s a quick overview of each Performance KPI:
19. Dock-to-Stock Cycle Time

This metric tracks the time taken from when goods arrive at the warehouse dock until they are stocked in their designated locations. It's an important measure of the efficiency of the receiving and put-away processes, with shorter cycle times indicating higher efficiency.
How to Calculate: Divide the total time it takes for all shipments to go from dock to stock by the number of shipments.
20. Labor Efficiency
Labor Efficiency measures the output produced by warehouse staff in relation to the amount of input (in terms of labor hours) used. This KPI is used to assess how effectively labor resources are being utilized within the warehouse operations.
How to Calculate: Divide the total labor costs by the total number of orders processed.
21. Warehouse Capacity Usage
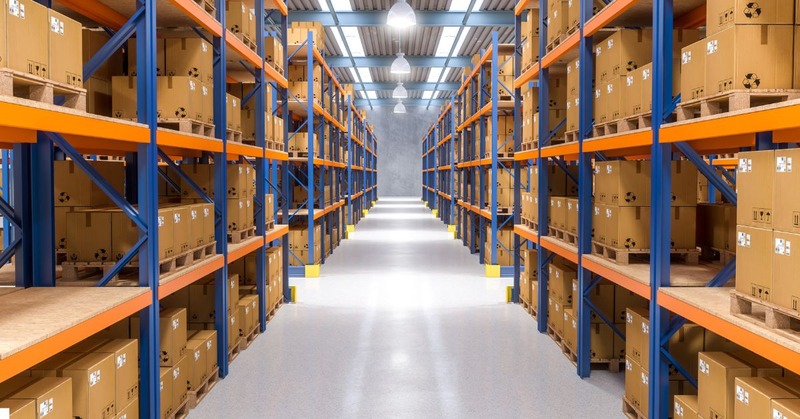
Warehouse Capacity Usage calculates the percentage of the warehouse space that is currently being used versus the total available space. It helps in understanding how efficiently the warehouse is utilizing its space and can aid in planning for expansion or reorganization to optimize space usage.
How to Calculate: Divide the amount of space currently being used by the total available space in the warehouse, then multiply by 100%.
E-Commerce KPIs
E-Commerce KPIs are crucial for online retail operations, focusing on the efficiency and reliability of fulfilling online orders.
These metrics are vital for ensuring customer satisfaction, optimizing logistics, and maintaining competitive advantage in the fast-paced world of eCommerce.
Here's a brief overview of the E-Commerce KPIs:
22. Order Fill Rate
The Order Fill Rate measures the percentage of customer orders that are fulfilled from stock available at the time of order placement. It's a critical metric for assessing inventory management efficiency and the ability to meet customer demand without delays.
How to Calculate: Divide the number of orders fulfilled in the first shipment by the total number of orders fulfilled and multiply by 100.
23. On-time Delivery
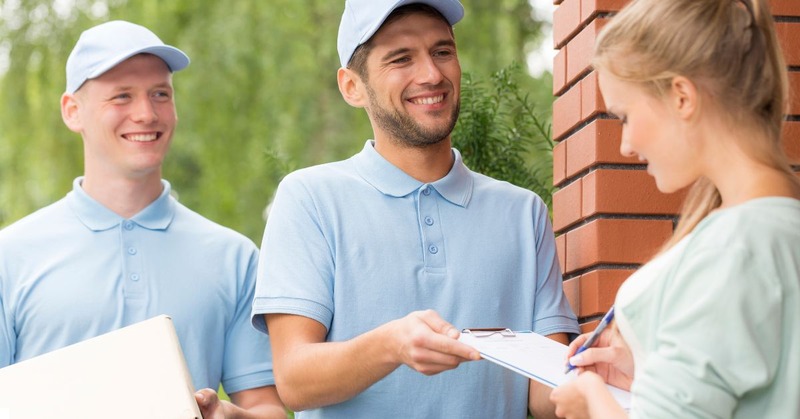
On-time Delivery tracks the percentage of orders delivered to customers within the promised delivery timeframe. High on-time delivery rates are essential for maintaining customer trust and satisfaction, directly impacting repeat business and brand reputation.
How to Calculate: Divide the sum of delivery time deviations for all orders by the total number of orders with promised delivery time, and then multiply by 100.
24. Time in Transit
Time in Transit measures the average duration it takes for an order to be delivered to the customer from the moment it leaves the warehouse. This KPI helps evaluate the efficiency of the shipping process and the performance of logistics partners, influencing customer satisfaction with delivery service levels.
What Can I Do to Improve My Warehouse's KPIs?
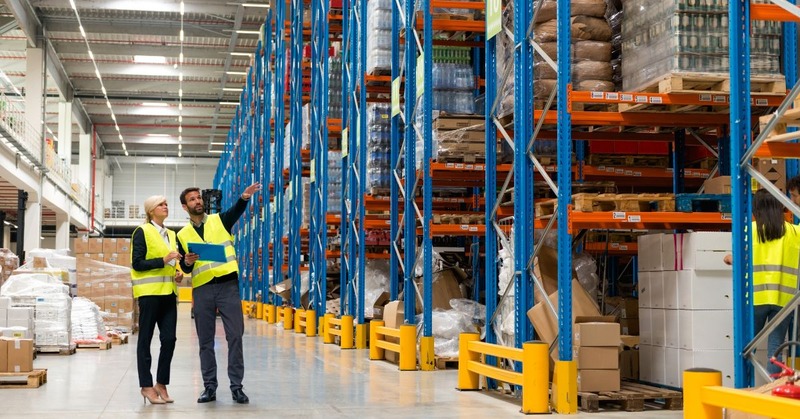
Improving your warehouse's Key Performance Indicators (KPIs) is essential for increasing operational efficiency, enhancing customer satisfaction, and driving profitability. Here are the top 5 actionable tips to help you enhance your warehouse KPIs effectively:
Invest in Technology and Automation
Adopting advanced technologies like Warehouse Management Systems (WMS), automated picking tools, and RFID tracking can dramatically improve accuracy and efficiency across inventory management, receiving, put-away, and order fulfillment processes.
Streamline Inventory Management
Implement Just-In-Time (JIT) inventory strategies to minimize carrying costs and boost inventory turnover. Conduct regular cycle counts and utilize technology for real-time inventory tracking to maintain high inventory accuracy and reduce shrinkage.
Optimize Labor Management
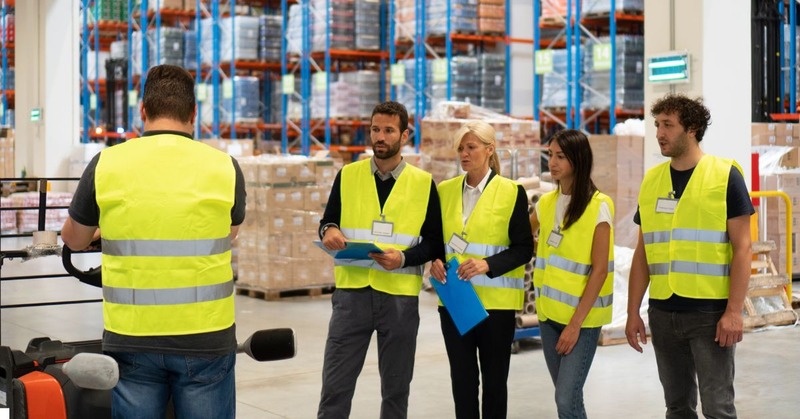
Focus on comprehensive employee training programs to ensure staff are proficient in the latest warehouse operations and technologies. Enhanced training and engagement lead to improved labor efficiency, accuracy, and overall warehouse performance.
Implement Lean Warehousing Principles
Adopt lean methodologies to eliminate waste and streamline operations. Continuous improvement initiatives can lead to significant enhancements in processing times, labor efficiency, and space utilization.
Enhance Safety and Workplace Environment
Regular safety training and a strong emphasis on maintaining a safe working environment reduce accidents and improve morale. A focus on safety contributes to better operational performance and longer periods without workplace incidents.
Conclusion
Using Packiyo's Warehouse Management System can boost your warehouse's efficiency and accuracy, positively affecting important performance measures.
If you want to know more about how Packiyo works, then we highly encourage you to talk to us so that we know what problems we're going to solve.
We also recommend that you read through our blog if you want to explore more topics such as 'What is Wave Picking?' and 'Pick and Pack Explained.'
In conclusion, warehouse KPIs serve as a compass for operational improvements, guiding warehouses toward higher efficiency, better customer service, and optimized cost management.
They are indispensable tools for modern warehouse management, enabling businesses to stay competitive in a fast-paced market.
We hope that we've helped you understand this topic, and we're looking forward to seeing you in our next post!