Imagine it's a hectic Monday at your warehouse and a critical piece of equipment breaks down unexpectedly, causing delays and added costs. Frustrating, right?
You're not alone in this struggle. Many warehouse managers face these challenges, affecting both productivity and expenses. But what if you could prevent these disruptions with effective maintenance strategies?
From the definition to the step-by-step process—in this article, we'll guide you through everything you need to know about maintaining a warehouse.
So stick with us until the end so that you can transform your warehouse problems into solutions.
What is Warehouse Maintenance?
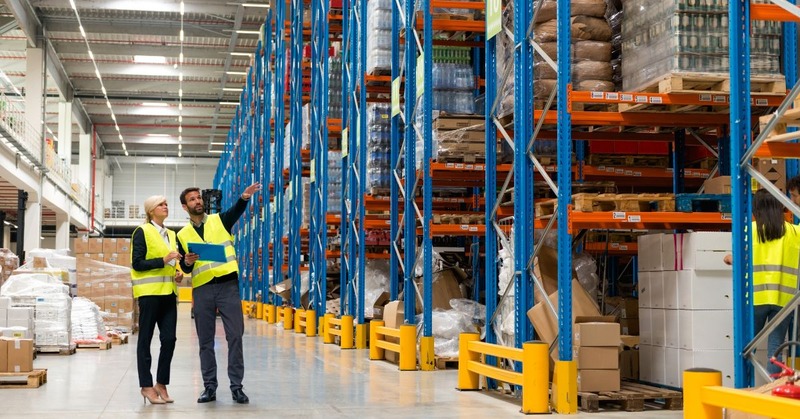
"Warehouse maintenance" is about keeping a warehouse running smoothly and safely. It includes regular checks, fixing things that break, and taking steps to prevent problems before they happen.
This covers everything from cleaning and organizing the space to servicing equipment and updating tech systems. Good maintenance stops equipment from failing, keeps things safe, and helps everything run more efficiently.
This not only keeps the warehouse itself in good shape but also ensures that the whole supply chain it supports keeps moving without costly interruptions.
Types
There are many types of warehouse maintenance, but these three are the most commonly applied:
Scheduled/Preventive Maintenance
This type involves routine activities that are planned and scheduled regularly. The main goal is to prevent unexpected equipment failures and ensure operations continue smoothly.
This could include both mechanical checks and general housekeeping tasks like trash removal and equipment cleaning.
Inspections
Regular inspections are crucial for spotting potential issues early on before they escalate into more significant problems.
This type of maintenance should focus on areas such as overall cleanliness, waste disposal systems, the efficiency of the receiving and loading processes, and compliance with regulations (like FDA standards for applicable products).
Training
An efficient warehouse relies heavily on its workforce. Providing regular training helps workers understand and safely operate equipment, and educates them on maintenance practices.
This not only enhances safety but also empowers the workforce to identify and report potential issues promptly.
Why is Warehouse Maintenance Important?
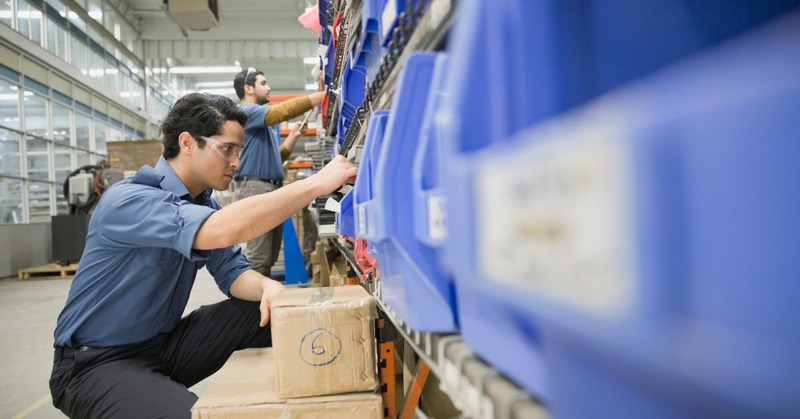
Basically, keeping a warehouse in shape goes way beyond just a tidy space. It's all about making sure everything in your supply chain runs smoothly, supports your business as it grows, and delivers what your customers expect, both quickly and safely.
But to explain further, you need to read the key points below:
Operational Efficiency
Keeping up with regular maintenance means all your gear and processes stay in tip-top shape, avoiding any hiccups.
This is super important for keeping things moving smoothly from start to finish, especially if your business is growing fast and you're dealing with a lot of orders. It keeps everything running like a well-oiled machine.
Safety and Compliance
Making sure your warehouse is well-maintained is key to keeping everyone safe at work.
Regular check-ups and fixes help avoid accidents and make sure everything meets safety standards, protecting your team and steering clear of any legal troubles.
Cost Management
Good maintenance doesn’t just keep things running smoothly; it also saves you money.
By preventing equipment from breaking down and making sure machines last longer, you can cut down on expensive repairs and replacements.
Plus, when your operations are running efficiently, you won’t have to keep more inventory than necessary, which helps in reducing storage costs.
What Happens When You Neglect Doing Warehouse Maintenance?
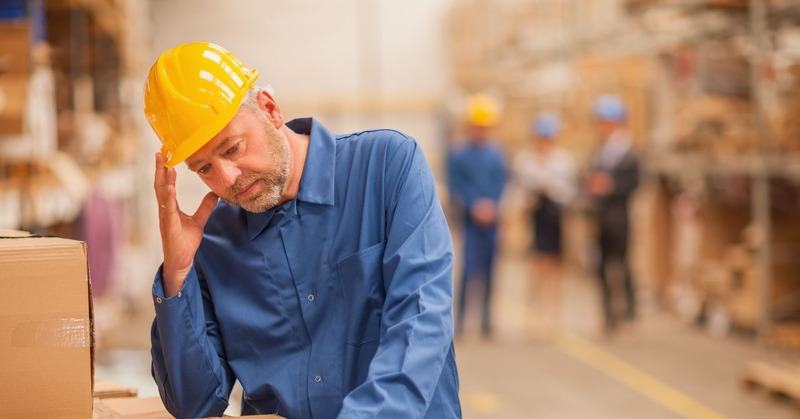
These are several issues that can arise if you ever decide not to keep up with your warehouse's maintenance:
Increased Operational Costs
Neglecting maintenance can cause machinery and equipment to break down more frequently, leading to higher repair costs and potential downtime, which affects productivity.
This can also increase the cost of operations, as more resources are needed to address these failures.
Safety Hazards
Without regular maintenance, the risk of accidents and injuries in the warehouse increases significantly. This can lead to serious injuries or even fatalities, as well as legal issues and increased insurance premiums.
Inventory Issues
Poor maintenance can disrupt the orderly storage and management of inventory. This can result in misplaced or lost items, inaccurate inventory counts, and difficulties in retrieving stock.
This disorganization can lead to missed sales opportunities due to items being out of stock when they are actually on-site but unaccounted for.
How to Maintain a Warehouse

Having grasped the definition, importance, and consequences of warehouse maintenance, let's now go through the proper ways and steps on how you can achieve that tip-top shape you're longing for.
1. Implement a Comprehensive Maintenance Schedule
Establish a detailed schedule that includes regular inspections and preventative maintenance to prevent potential issues. This should be coordinated during off-peak hours or scheduled downtimes to minimize disruption, ensuring that all critical equipment and areas are covered systematically.
2. Utilize Advanced Warehouse Management Systems (WMS)
Choose a WMS that enhances operational efficiency through automation and provides in-depth analytics. This system should help in tracking operational performance, scheduling maintenance tasks, and streamlining various warehousing operations, which can significantly reduce manual errors and operational downtime.
3. Develop a Robust Training Program
Invest in comprehensive training for all staff on maintenance awareness and safety protocols. This should include seminars on how to identify and troubleshoot potential issues. Empowering your employees with this knowledge helps in early detection of problems, maintaining safety, and enhancing operational efficiency.
4. Maintain Cleanliness and Organization
Regular cleaning and systematic organization of the warehouse should be mandatory. Implement protocols that ensure every item is returned to its designated place. This not only maintains order but also reduces the time spent locating items and prevents accidents caused by clutter.
5. Continuously Update Maintenance Protocols
Regularly review and refine your maintenance strategies to adapt to new technologies, changes in operations, or feedback from maintenance teams. This might involve adjusting maintenance schedules based on the actual needs and wear patterns observed in the equipment.
6. Establish a Preventative Maintenance Program
Identify critical equipment and set up a routine maintenance schedule based on manufacturer recommendations and historical data. Utilize a preventive maintenance plan that includes detailed checklists and schedules for all equipment, ensuring consistent upkeep and reducing the likelihood of unexpected failures.
7. Adopt CMMS Software
Implement Computerized Maintenance Management System (CMMS) software to automate and organize maintenance tasks. This tool can help manage work orders, track equipment status, maintain inventory levels of spare parts, and ensure compliance with safety standards, all within a predefined budget.
8. Standardize Maintenance Procedures
Create standard operating procedures (SOPs) and maintenance checklists for all repetitive tasks. This standardization helps in maintaining consistency in maintenance practices and ensures that all procedures are performed correctly and efficiently.
9. Engage and Communicate with Your Team
Regular interaction with the warehouse staff can provide insights into daily challenges and potential areas of improvement. Encourage feedback and involve them in decision-making processes related to maintenance and safety protocols.
10. Leverage Data for Continuous Improvement
Utilize the data collected from various systems to monitor performance and identify areas for improvement. Regular analysis of this data can help in optimizing maintenance schedules and procedures based on actual usage patterns and equipment performance.
FAQs
Got any more questions about maintaining a warehouse? We might have answered some of them below!
What are the most critical areas to focus on during warehouse maintenance inspections?
Key areas to focus on during warehouse maintenance inspections include electrical systems to prevent hazards, roofing to avoid leaks and structural damage, dock areas to ensure safe loading and unloading, and storage systems to maintain organization and prevent accidents. Regular checks of these areas help in identifying and mitigating potential risks early.
How often should warehouse maintenance be scheduled?
Warehouse maintenance schedules can vary based on the equipment and operations but generally, preventive maintenance should be conducted monthly for general checks and quarterly for more in-depth inspections. Critical equipment might require more frequent checks depending on usage patterns and manufacturer recommendations.
What are the common signs that indicate a need for immediate maintenance in a warehouse?
Signs that indicate the need for immediate maintenance include unusual noises from machinery (indicating potential failure), leaks (which can cause slips or damage to goods), visible wear and tear on equipment, and operational inefficiencies like sudden slowdowns in production lines or logistics.
Conclusion
In conclusion, maintaining an efficient and safe warehouse is crucial, and leveraging a powerful Warehouse Management System like Packiyo can make a big difference.
Packiyo streamlines your warehouse operations with features that support regular maintenance checks, simplify inspections with mobile access, and enhance worker training through its intuitive interface. It also integrates seamlessly with other maintenance software, ensuring that all your systems work together smoothly.
Check out our blog if you want to explore similar topics like 'why is shipping taking so long', 'how to ship fragile items', and more. Alternatively, contact us if you want to learn more about Packiyo as a whole.
Again, through these practices, warehouse maintenance becomes an integral part of operations, contributing to a safer, more efficient, and productive environment.
We hope we've helped you understand how to maintain your warehouse. Don't hesitate to comment below with your thoughts on this topic.
Stay safe!