Wave picking and batch picking are two of the most well-known picking methods, and as warehouse managers, you should know the difference between these two so that you can create a more concrete picking plan for your warehouse.
But... which is better between batch and wave picking? In this article, we'll let you in on the answer.
Wave picking may be a good strategy where orders are grouped and processed in waves; on the other hand, batch picking involves gathering items for multiple orders in one go.
Each method has its own pros and cons, and the best choice often depends on balancing the specific demands of your operations with the benefits each picking strategy offers.
If you want to read more about this topic, then read further. We'll discuss everything you need to know about which is better between wave picking and batch picking.
Let's get into it.
Wave Picking and Batch Picking Overview
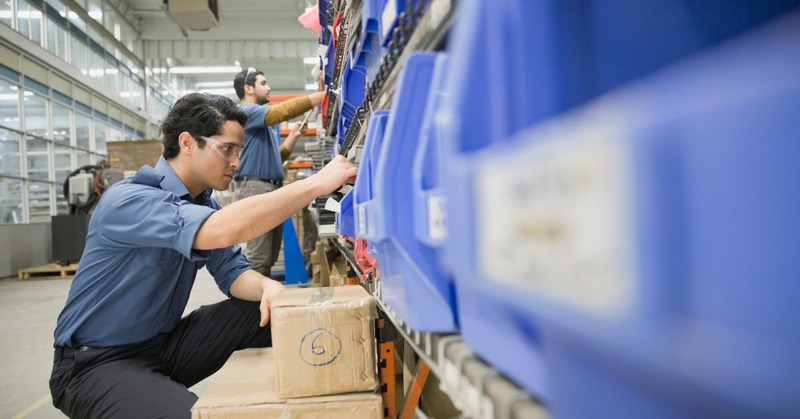
Before anything else, let's first go through the definitions of what makes up wave and batch picking.
What is Wave Picking?
Wave picking is a sophisticated warehouse management strategy that involves organizing the order picking process into distinct "waves" to maximize efficiency and coordination.
This method groups orders based on certain shared characteristics, such as product type, delivery route, or the type of equipment needed for picking.
By doing so, it minimizes redundant trips to the same locations in the warehouse and aligns picking activities with specific operational timelines, such as work shifts or transport schedules.
Example:
Consider a warehouse that handles a variety of products, including electronics, clothing, and perishables. In a single day, the warehouse might receive orders that vary greatly in terms of item type and delivery urgency.
Wave picking would allow the management to create different waves throughout the day — perhaps one wave for all electronics that require careful handling, another for clothing items, and a third for perishables that must be processed quickly.
This way, items that require similar handling, packaging, or are located physically close to each other are picked during the same wave, reducing the time and effort spent on logistics.
Pros:
- Efficiency in operations: By grouping similar orders, wave picking reduces the time spent moving between different areas of the warehouse.
- Enhanced coordination: Scheduling waves according to shipping deadlines and workforce availability can lead to better use of labor and resources.
- Improved accuracy: With fewer distractions and less congestion in aisles, the likelihood of picking errors decreases.
Cons:
- Complex scheduling: Wave picking requires precise planning and a deep understanding of all operational variables, which can complicate logistics.
- Risk of idle time: If waves are not properly aligned with other activities, it can lead to periods where workers or equipment are not being used efficiently.
- Dependency on forecasts: Successful wave picking relies heavily on accurate predictions of order volumes and processing times, making it less flexible to unexpected changes.
What is Batch Picking?
Batch picking is a streamlined order fulfillment method used in warehousing where a picker collects items for multiple orders in one go, based on shared product types or SKU.
This approach reduces the number of trips a picker must make to the same pick locations, making it highly efficient for fulfilling multiple orders that share common items.
Example:
Imagine a warehouse that deals with frequent orders for office supplies.
If orders come in for 50 pens, 30 pencils, and 40 staplers from various clients, a picker using batch picking would collect all pens in one trip, all pencils in another, and all staplers in a third.
This method reduces the walking distance and time spent on picking individual items for each order, thus accelerating the order fulfillment process.
Pros:
- Increased efficiency: Collecting items in batches minimizes the walking and searching time, speeding up the overall picking process.
- Reduced fatigue: Less time walking and moving between locations means lower physical strain on warehouse workers.
- Simplified sorting: By picking common items in bulk, the sorting and packaging process can be streamlined, as items are already grouped by type.
Cons:
- Potential for picking errors: Handling multiple orders simultaneously can increase the likelihood of mistakes in item quantities or order details.
- Limited flexibility: Batch picking is less effective for orders that vary significantly in item type or size, as it's optimized for similar small items.
- Sorting required: After collecting the items, there's a need for additional sorting to ensure that each order is correctly assembled from the batched items.
How Does Batch Picking and Wave Picking Compare to One Another?

Now that we understand what wave and batch picking are independently, let's go through the similarities and differences between them to know which method is better.
Similarities
Both batch picking and wave picking are designed to enhance efficiency and accuracy in warehouse operations. They aim to optimize the order fulfillment process by reducing the physical strain on workers and minimizing the time spent traveling within the warehouse.
Here’s a breakdown of their key similarities:
Efficiency Focus
Both methods aim to streamline the picking process, reducing the time it takes for workers to collect items and prepare them for shipping.
Reduced Travel
By grouping items or orders in a manner that minimizes back-and-forth movement, both strategies cut down on the distance that pickers need to travel.
Enhanced Accuracy
Organizing the picking process helps reduce the likelihood of errors, as pickers can focus on specific groups of items or orders, reducing confusion and potential for mistakes.
Differences
While batch picking and wave picking share some goals, their approaches and implementations are quite distinct, catering to different operational needs and challenges:
Organization Strategy
Batch picking groups items that are part of multiple orders but similar in type or location, allowing pickers to collect all needed items in one go. Wave picking, on the other hand, groups orders into waves based on criteria like delivery schedules or product type, and these waves are picked at scheduled times throughout the day.
Flexibility vs. Scheduling
Batch picking offers more flexibility as it primarily focuses on the efficiency of the picking process itself without strict adherence to timing. Wave picking is highly structured, with scheduled waves that must align with other logistical activities, such as shipping or shift timings.
Complexity and Planning
Wave picking requires more intricate planning and is heavily dependent on accurate forecasts and scheduling to align with broader operational timelines. Batch picking is generally simpler to implement as it focuses more on the immediate efficiency of picking items that are physically or categorically similar, without the same level of dependency on external schedules.
Suitability
Batch picking is ideally suited for environments with a high volume of orders that include similar items, making it less effective for varied item types. Wave picking is better suited for larger, more complex operations where orders vary significantly and there is a need to coordinate picking activities with other warehouse operations and shipping schedules.
Understanding these similarities and differences can help businesses choose the most appropriate picking strategy based on their specific operational requirements, warehouse layout, and the nature of the items they handle. Each method has its strengths and is best applied in scenarios that match its unique advantages.
Which is Better Between Wave Picking and Batch Picking?
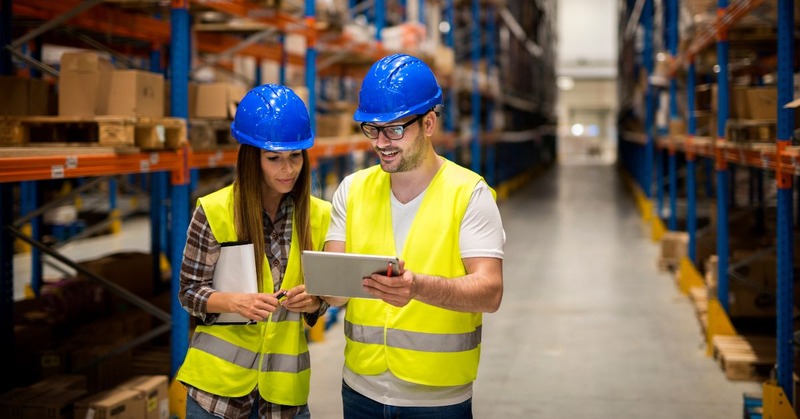
Choosing between wave picking and batch picking depends on several operational factors specific to your warehouse environment, the nature of your orders, and your logistical priorities.
Below are the factors you should consider to determine which method is more suitable for your operations.
Choose Wave Picking If:
Complex Logistics and Varied Order Profiles
If your warehouse processes a wide variety of products and deals with complex shipping schedules, wave picking can provide the structured approach needed to manage such complexity effectively.
Need for Tight Scheduling
Wave picking is ideal if your operations are heavily dependent on aligning picking activities with specific transport schedules or labor shifts. This method helps in managing labor more efficiently by scheduling waves when workers are available and reducing idle time.
High Demand for Coordination
Large warehouses that require coordination between various departments (such as receiving, picking, and shipping) benefit from wave picking because it allows for better synchronization across activities.
Requirement for Scalability in Peak Times
During peak operational periods, wave picking can help manage increased volumes efficiently by pre-planning waves based on anticipated order inflows and customer delivery requirements.
Choose Batch Picking If:
High Volume of Similar Orders
Batch picking is most effective when many orders contain similar items. This method reduces the time and effort spent on picking by grouping similar SKUs, making it easier and faster to fulfill multiple orders simultaneously.
Simpler Operational Needs
For smaller or less complex warehouses, batch picking offers a straightforward way to enhance efficiency without the need for intricate scheduling or high-end software systems.
Flexibility in Order Processing
If your operation values flexibility over strict scheduling, batch picking allows pickers to respond dynamically to order requirements without the constraints of scheduled waves.
Efficiency Overhead Reduction
When the goal is to minimize movement within the warehouse and reduce physical strain on workers, batch picking effectively cuts down the distance traveled per order.
Understanding these factors can guide you in choosing the right picking strategy to enhance operational efficiency, reduce costs, and improve order accuracy and customer satisfaction in your warehouse. Each method has its advantages, and the best choice often depends on balancing the specific demands of your operations with the benefits each picking strategy offers.
FAQs
Got more questions about comparing batch and wave picking? Well, we might have tackled some of them below:
Can wave picking and batch picking be combined in a single warehouse operation? Yes, combining wave and batch picking is effective in warehouses handling a variety of order types and sizes. This hybrid approach provides flexibility to adapt to changing demands and allows for optimal use of each method: wave picking during busy periods and batch picking for simpler tasks.
How do wave picking and batch picking impact overall customer satisfaction? Wave and batch picking both aim to improve order accuracy and delivery speeds, key factors for enhancing customer satisfaction. These methods reduce delivery times and improve the precision of orders, which can lead to greater customer loyalty and trust.
What types of products or industries are best suited for wave picking or batch picking? Wave picking works well for industries with diverse product types and varying order sizes, such as electronics or automotive parts, due to its scheduling flexibility. Batch picking is ideal for sectors like pharmaceuticals and food and beverage, where orders typically include small, similar items and occur frequently.
Conclusion
In conclusion, deciding between wave and batch picking largely depends on the specific needs of your warehouse operations, including the types of orders processed, the layout and size of the warehouse, and the flexibility required in the picking process.
Each method has its strengths, and choosing the right one can significantly impact operational efficiency and customer satisfaction.
Using a robust Warehouse Management System like Packiyo can significantly improve your warehouse operations.
Our key features, such as Automation Co-Pilot and Mobile Smart Pick, streamline the implementation of wave and batch picking, enhancing their effectiveness.
The system automates the sorting and batching of orders and provides real-time data to support quick decision-making, ensuring your warehouse operates efficiently.
Packiyo is adaptable to both picking strategies, making it an essential tool for optimizing your workflows and increasing productivity.
If you have any concerns or questions related to this topic, don't hesitate to reach out to us. If you want to read more about topics like this one, then be sure to check out our blog where we've discussed things like 'What does carbon neutral shipping mean?', 'What is a milk run?', and more.
We hope that we've helped you understand what batch and wave picking are, and we look forward to seeing you in our next post.
Take care!