If you're running a warehouse operation, you've likely faced challenges with managing inventory, fulfilling orders accurately, and maintaining efficient workflows.
These issues can slow down your operations, increase costs, and frustrate both your staff and customers. Searching for ways to streamline your processes, you might have come across the concept of zone picking.
Zone picking promises to enhance efficiency by dividing the warehouse into specific zones, with pickers assigned to each area. But the question remains: is zone picking the right solution for your warehouse?
This article will explore the benefits and challenges of zone picking and how Packiyo's Warehouse Management System can help you overcome these hurdles to achieve a more efficient and accurate order fulfillment process.
What is Zone Picking?
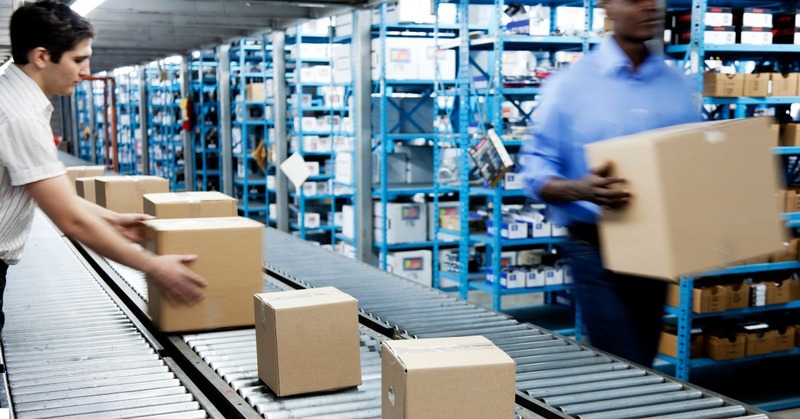
Zone picking, often referred to as "pick and pass," is a warehouse order fulfillment method where the storage area is divided into distinct sections called zones.
How It Works
Each zone is designed to handle specific types of products or activities, such as handling bulk items, flammable materials, or high-demand products.
This method is analogous to an assembly line in that each zone specializes in picking certain parts of an order, which are then passed along to the next zone or consolidated before shipping.
Example
Imagine a large distribution center that handles a variety of consumer goods. The warehouse is segmented into four zones based on product type and picking process:
- Zone 1: High Demand Items - Contains frequently ordered items like toiletries and small electronics. Pickers in this zone use fast picking methods like flow racks or automated systems to quickly process orders.
- Zone 2: Bulk Items - Houses large or heavy items that require equipment like forklifts. Here, items are picked less frequently and require more space.
- Zone 3: Fragile Goods - Dedicated to items that need special handling, such as glassware or electronics. This zone uses specialized packing techniques to ensure safety during transit.
- Zone 4: Cold Storage - Used for items requiring refrigeration like food products or certain chemicals. The environment here is controlled to maintain product integrity.
An order might include a mix of items such as a bottle of shampoo from Zone 1, a pack of batteries from Zone 3, and a frozen pizza from Zone 4.
Each product is picked by the zone specialist and sent to a consolidation area where the order is assembled and prepared for shipping.
This method optimizes picking efficiency by reducing travel time for pickers within their zones and allows for specialization in product handling, leading to faster order processing and reduced errors.
Types
Sequential Zone Picking
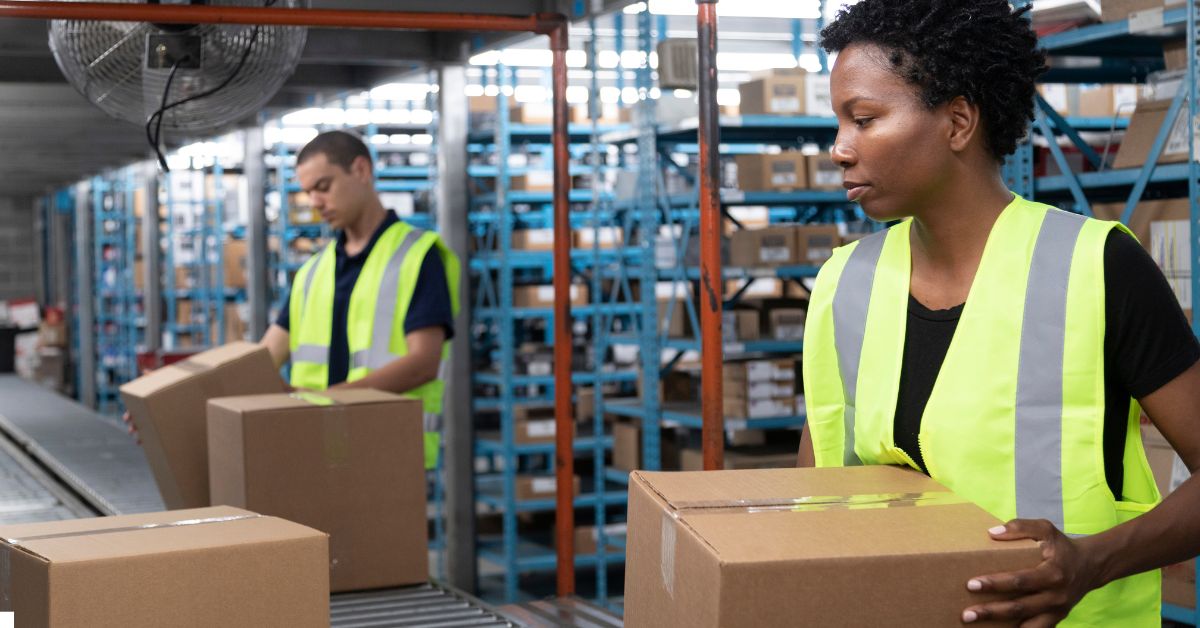
Sequential zone picking involves each picker handling items within their assigned zone before passing them along to the next zone.
This method ensures a smooth, continuous flow of items, often supported by conveyors or manual transfer, making it efficient for large orders that require assembling multiple components sequentially.
Simultaneous Zone Picking
Simultaneous zone picking speeds up the process by having multiple pickers in different zones work on the same order at once.
Each picker collects items from their zone, with all components then brought together for final assembly. This approach reduces waiting times but may require extra steps to consolidate items before shipping.
Pros and Cons
Pros
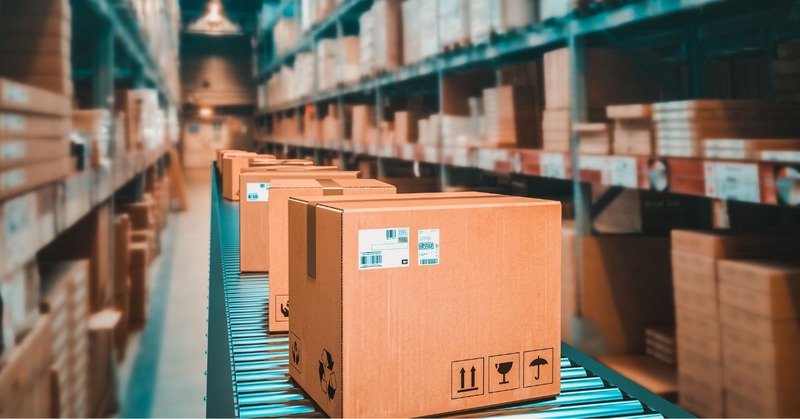
- Increased Efficiency: Zone picking minimizes travel time for pickers as they operate within a confined area, leading to quicker fulfillment processes.
- Specialization: Pickers become highly familiar with the SKUs in their zone, improving accuracy and speed.
- Flexibility: Zones can be adjusted based on changing inventory needs or business goals, allowing for different picking strategies like batch or single order picking within each zone.
- Reduced Congestion: With fewer pickers moving between zones, there's less traffic, which decreases the likelihood of bottlenecks.
- Scalability: Particularly beneficial for large warehouses with a diverse range of products, allowing for more tailored picking strategies that match the specific needs of different item types.
Cons
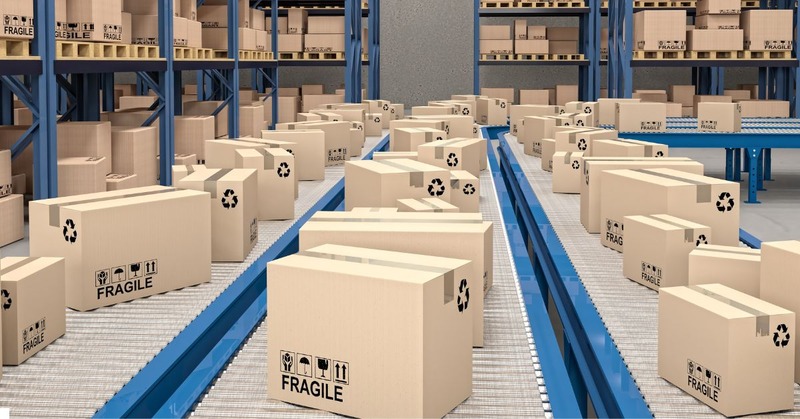
- Multiple Touch Points: Items may pass through several zones before completion, increasing the risk of errors due to multiple handoffs.
- Error Identification Challenges: When errors occur, pinpointing responsibility can be difficult because multiple pickers across different zones handle the items.
- Additional Steps in Fulfillment: Especially in simultaneous picking, items picked from various zones need to be consolidated, adding complexity to the outbound process.
- Fixed Scheduling: Zone picking usually requires a single scheduling period per shift, which can delay processing of orders received after the cutoff time.
- Workload Imbalance: If order volumes are uneven across zones, it can lead to idle time for some workers while others are overburdened, potentially leading to uneven wear and worker fatigue.
This covers everything you need to know about zone picking. Next, we'll compare zone picking to other methods so you can decide if it's the right choice for you.
How Does Zone Picking Compare to Other Picking Methods?
Below, we'll discuss different picking methods and how they compare to zone picking. Let's explore each one:
Discrete Picking Compared to Zone Picking
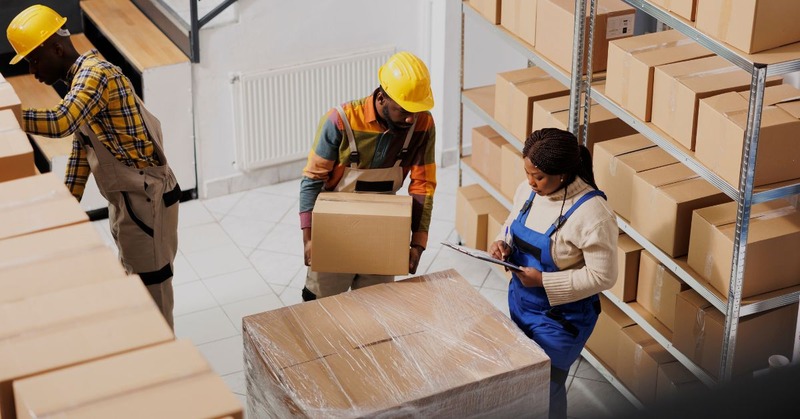
Discrete picking involves a picker completing one entire order at a time, moving SKU by SKU until the order is finished.
This method is straightforward but often inefficient for larger operations due to its labor-intensive nature.
Compared to zone picking, discrete picking requires more travel within the warehouse, as a picker must traverse the entire facility to gather all items for a single order.
In contrast, zone picking confines pickers to specific areas, reducing travel time and potentially increasing efficiency, particularly in large warehouses with diverse SKUs.
Batch Order Picking Compared to Zone Picking
Batch order picking groups multiple orders together based on similar SKUs, allowing pickers to collect the same item for several orders simultaneously, which can significantly cut down on travel time.
This method is most beneficial in operations that handle orders with similar items frequently.
Zone picking, while also aiming to reduce travel time, does so by assigning pickers to specific zones rather than grouping orders.
This can lead to less flexibility compared to batch picking where similar items across different orders can be picked in one pass.
Wave Picking Compared to Zone Picking
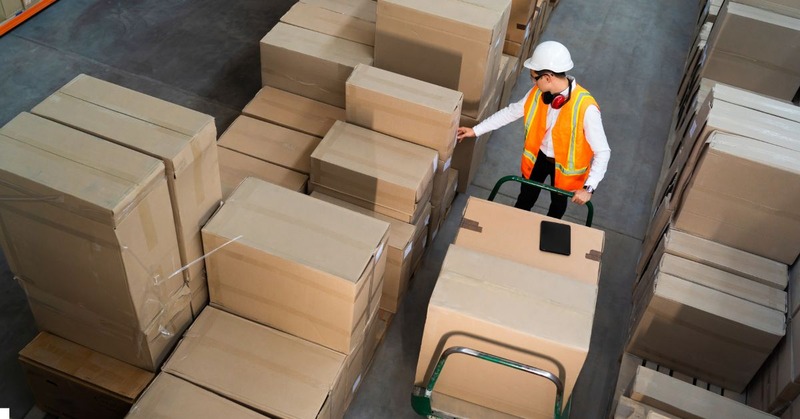
Wave picking organizes the picking process into waves, allowing pickers to handle a large set of orders in a single walkthrough of a facility.
This method can reduce travel time and is particularly suited for B2B operations with high-volume orders.
Unlike zone picking, which can restrict pickers to specific areas and potentially limit flexibility, wave picking allows for a more dynamic and comprehensive approach as pickers traverse different zones based on the wave's requirements.
If you want to check out more topics related to this, try reading through our case picking article.
Waveless Picking Compared to Zone Picking
Waveless picking is a dynamic version of wave picking where batches are continuously updated with new orders as older ones are completed.
This method ensures a consistent flow of work and is beneficial for environments demanding rapid shipping, like e-commerce.
Zone picking, on the other hand, involves static zones which may lead to delays if not all zones are equally busy.
Waveless picking offers more flexibility and continuous productivity compared to the more segmented approach of zone picking.
Overlapping Waves Compared to Zone Picking
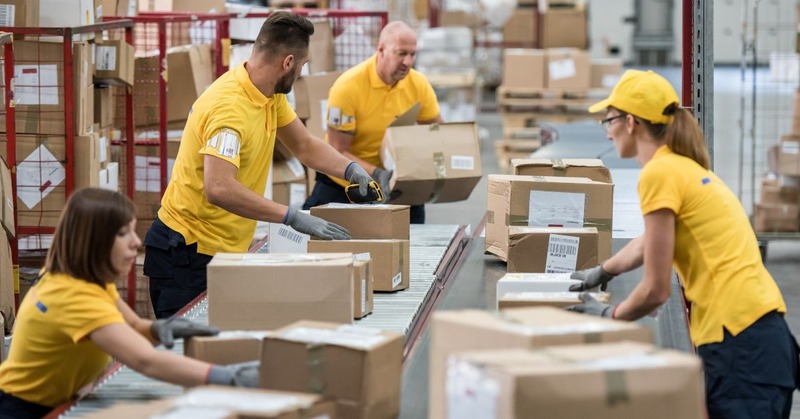
Overlapping waves order picking allows new waves to start before previous ones are completed, smoothing out the productivity levels across the operation.
This contrasts with zone picking, where each zone may operate independently, possibly leading to uneven workloads and productivity levels.
Overlapping waves can thus offer a more balanced and continuous picking flow than zone picking, which might experience downtime depending on the order flow within each zone.
Each method has its advantages based on warehouse needs, inventory nature, and order volume. Zone picking is effective in large, varied warehouses but may not always be the best choice depending on operational goals and order flow characteristics.
Signs You Need Zone Picking in Your Warehouse
If you're considering implementing zone picking in your warehouse operations but aren't sure if it's the right move, here are some signs that this method might be beneficial for you:
High SKU Variety
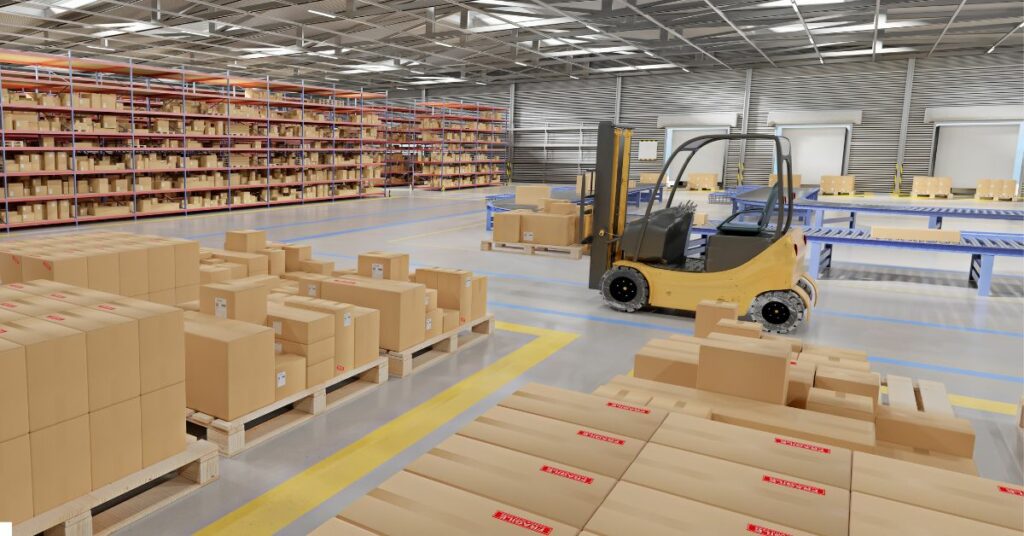
If your warehouse deals with a large number of SKUs, especially those with unique characteristics or special handling requirements, zone picking can be extremely beneficial.
This method reduces travel time and increases picking efficiency because workers become familiar with the SKUs in their specific zone.
Frequent Order Delays and Mistakes
If you're experiencing frequent delays in order fulfillment or a high rate of picking errors, zone picking might help.
By dividing the warehouse into zones, each picker becomes more familiar with their assigned area, potentially reducing errors and improving overall order accuracy.
Need for Improved Labor Efficiency
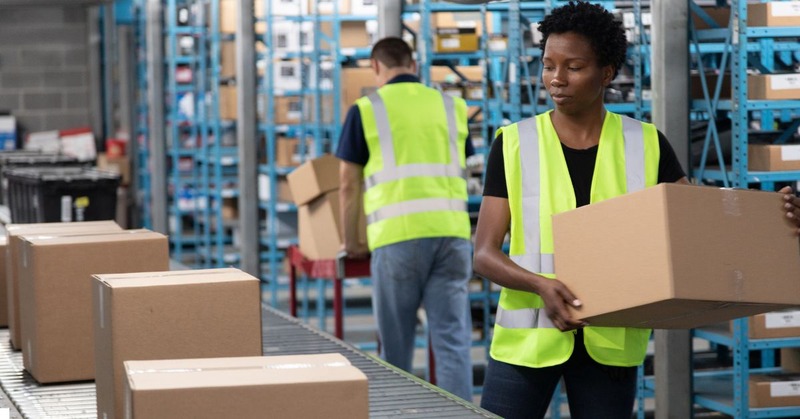
Zone picking can significantly improve labor efficiency. It minimizes the distance each picker travels, allowing them to spend more time picking and less time moving around the warehouse.
If you find that your pickers are spending a substantial portion of their time traveling within the warehouse, zone picking could be a solution.
Congestion and Bottlenecks in Picking Areas
If your warehouse often experiences congestion and bottlenecks, especially in areas with high picking activity, zone picking can help alleviate these issues.
By assigning pickers to specific zones, it reduces the number of workers moving through the warehouse at any given time, thus minimizing traffic and improving safety and efficiency.
Scalability Concerns
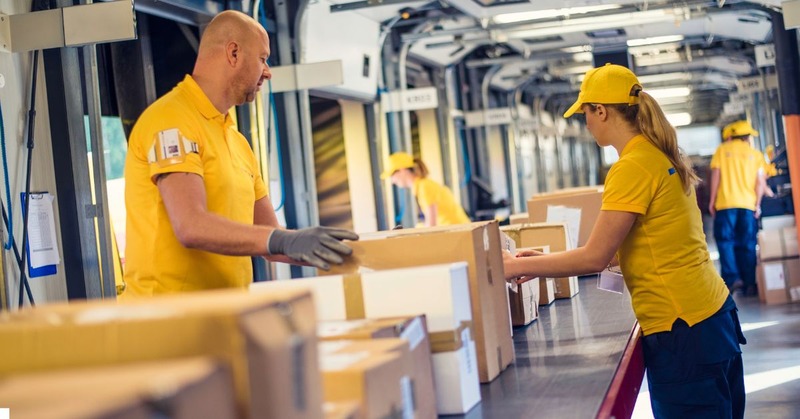
As your business grows, scalability becomes crucial. Zone picking allows for better scalability by making it easier to manage an increasing number of orders and SKUs. It simplifies the process of adding more zones or adjusting existing ones to accommodate growth.
These signs can help you decide if zone picking is right for your warehouse. If several apply, it might be time to consider implementing or optimizing zone picking to boost efficiency, accuracy, and productivity.
FAQs
Before ending our discussion on zone picking, here are some questions that may have crossed your mind:
What technologies can enhance zone picking efficiency?
Technologies like Warehouse Management Systems (WMS) and Radio Frequency Identification (RFID) can significantly boost the efficiency of zone picking. WMS can optimize pick paths and manage inventory dynamically, while RFID allows for real-time tracking of items as they move between zones, reducing errors and speeding up the process.
How do you determine the optimal number of zones in a warehouse?
The optimal number of zones in a warehouse depends on several factors, including the variety and volume of SKUs, the physical layout of the warehouse, and the daily volume of orders. Analyzing historical data and using simulation software can help in configuring zones to balance workload and maximize efficiency.
Can zone picking be integrated with other picking strategies?
Yes, zone picking can be integrated with other strategies like batch picking, wave picking, or pick-to-light systems to form hybrid methods. This integration can help address specific operational challenges, such as varying order sizes and SKU velocities, making the picking process more flexible and efficient.
What training is required for workers in a zone picking system?
Workers in a zone picking system require training on the specific SKUs within their assigned zones, the use of any relevant picking technologies, and the overall workflow of the warehouse. Ongoing training is also important as inventory and processes change.
How does zone picking impact inventory management?
Zone picking can improve inventory accuracy and control by reducing the movement of items across the warehouse. It simplifies tracking and managing stock levels within each zone, facilitating more precise inventory forecasts and reducing the likelihood of stockouts or overstock situations.
Conclusion
For businesses fine-tuning their warehouse zone picking, mastering the complexities of inventory distribution, order fulfillment accuracy, and workflow efficiency is crucial.
Packiyo's Warehouse Management System offers targeted solutions to streamline these aspects of zone picking.
Our WMS boosts warehouse efficiency through our Mobile Smart Pick and Automation Co-Pilot, guiding pickers with real-time instructions, thus reducing travel time and errors.
Our advanced inventory management precisely aligns items based on characteristics like velocity, optimizing zone picking.
The system also includes Bulk Ship and Rapid Pack & Ship to alleviate bottlenecks and enhance shipping processes, while integrated analytics track picker productivity and order accuracy, supporting ongoing improvements.
If you're currently looking for related content, then don't hesitate and check out our blog, where we cover recent topics such as ‘ecommerce warehousing’, ‘voice picking’, and ‘supply chain bottlenecks’.
Again, we hope that we've helped you understand what zone picking is and how this can potentially help you enhance your picking efficiency.
If you need any more help, then don't hesitate to contact us here at Packiyo.